Non-ferrous metals
A Blockchain Solution for Cobalt Traceability
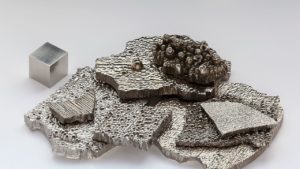
A global EV pioneer and one of the world’s leading battery makers are also part of the pilot. Tested in real operating conditions, from upstream cobalt production sites in the Democratic Republic of the Congo (DRC) to downstream electric vehicle production sites, the pilot will run until the end of 2021, with the roll-out of the final solution expected in 2022.
Assured through blockchain technology, the solution is a unique industry partnership between EV supply chain majors aiming to accelerate sustainable practices for every unit of cobalt mined, processed and used in end products. Founded by CMOC, ERG and Glencore and launched in 2019, Re-Source was later joined by Umicore, as well as a battery and EV company. It is designed with the direct input of responsible sourcing, and supply chain experts from all participating companies, proactively addressing the growing need for cobalt value chain visibility.
The collaboration between major cobalt industry players working in the DRC, deploys various technologies, including blockchain and Zero-Knowledge Proofs, to link digital flows with physical material flows on the ground. The ground-breaking solution is supported by boutique technology studio Kryha, which is experienced in carbon footprint and metals traceability and known for projects with the World Economic Forum.
To meet the consortiums’ mission of ensuring that all cobalt used in end products will be sustainably sourced, Re-Source integrates a comprehensive set of industrial sustainable mining and sourcing standards and frameworks, such as ICMM, RMI, IRMA CIRAF1, Copper Mark and others. The solution is therefore also exploring how aspects of the related GHG emissions along the value chain can be traced and disclosed.
In addition to EV supply chain majors, Re-Source is developed with the involvement of a broad group of industry advisors and stakeholders. It reflects their expectations about all aspects of sustainably sourced materials and is designed to be used by wide-ranging industry players.
Re-Source also has a direct link with the Battery Passport project of the Global Battery Alliance (GBA), through ERG, Umicore, Glencore and other Re-Source pilot partners, members of the GBA. The Battery Passport is aimed at transforming the entire value chain to make battery production more responsible and sustainable. The member companies believe that these projects support each other and together will deliver on the overarching agenda of increasing sustainability in the wider battery supply chain.
Marc Grynberg, CEO of Umicore, said: “I am proud to support Re-Source in developing a technology solution to assure traceability in the entire battery industry. For many years, Umicore has been a pioneer in promoting a sustainable value chain by only offering battery materials of a certified and ethical origin. Today, we share our expertise within this innovatory consortium and participate in the pilot to develop an industry-wide traceability technology, which is an important step towards a sustainable value chain for all batteries.”
Ivan Glasenberg, CEO of Glencore, said: “Blockchain technology offers us an unprecedented ability for traceability in the supply chain. Through this pilot, we are supporting the development of this tool for our customers who seek to understand and demonstrate the origin of the cobalt units in their products. But traceability is not enough on its own, it must be part of a wider industry effort to bring improvements to the entire cobalt supply chain. This starts with responsible sourcing compliance, for example through RMI; the collective use of wider ESG standards such as CIRAF and ICMM; and supporting the artisanal and small-scale mining (ASM) sector in the Democratic Republic of Congo (DRC) sector through multi-stakeholder initiatives like the Fair Cobalt Alliance (FCA).”
Sun Ruiwen, CEO of CMOC, said: “Re-Source is a very exciting development in global battery industry. As a global leading producer and trader of cobalt, CMOC and its trading affiliate IXM are committed to the responsible mining, processing and use of cobalt. We believe this initiative will help increase the transparency throughout the value chain. In the backdrop of the global energy transition and China pledging carbon neutrality by 2060, the battery industry is growing and expanding rapidly. A transparent and responsible supply chain, bringing together all stakeholders with this joint effort, will give end users greater confidence in cobalt as a raw material.”
Benedikt Sobotka, CEO of ERG and co-chair of the Global Battery Alliance, said: “Eurasian Resources Group prides itself on being a leading cobalt producer globally, operating the second-largest standalone cobalt production facility with a design capacity of 24 ktpa. As part of our continued efforts to ensure cobalt is responsibly sourced and processed, a key focus for ERG has been collaborating with leading public and private organisations to respond to the growing battery market powering the energy transition and the low carbon economy which is the biggest purchase order in history. Piloting the Re-Source solution is a vital milestone that brings us one step closer to unveiling the significant potential of batteries, while strengthening transparency and sustainability of battery materials across the value chain – also a mission of the Global Battery Alliance, where ERG is a founding member.”
A Blockchain Solution for Cobalt Traceability
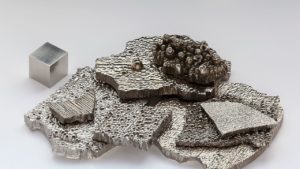
A global EV pioneer and one of the world’s leading battery makers are also part of the pilot. Tested in real operating conditions, from upstream cobalt production sites in the Democratic Republic of the Congo (DRC) to downstream electric vehicle production sites, the pilot will run until the end of 2021, with the roll-out of the final solution expected in 2022.
Assured through blockchain technology, the solution is a unique industry partnership between EV supply chain majors aiming to accelerate sustainable practices for every unit of cobalt mined, processed and used in end products. Founded by CMOC, ERG and Glencore and launched in 2019, Re-Source was later joined by Umicore, as well as a battery and EV company. It is designed with the direct input of responsible sourcing, and supply chain experts from all participating companies, proactively addressing the growing need for cobalt value chain visibility.
The collaboration between major cobalt industry players working in the DRC, deploys various technologies, including blockchain and Zero-Knowledge Proofs, to link digital flows with physical material flows on the ground. The ground-breaking solution is supported by boutique technology studio Kryha, which is experienced in carbon footprint and metals traceability and known for projects with the World Economic Forum.
To meet the consortiums’ mission of ensuring that all cobalt used in end products will be sustainably sourced, Re-Source integrates a comprehensive set of industrial sustainable mining and sourcing standards and frameworks, such as ICMM, RMI, IRMA CIRAF1, Copper Mark and others. The solution is therefore also exploring how aspects of the related GHG emissions along the value chain can be traced and disclosed.
In addition to EV supply chain majors, Re-Source is developed with the involvement of a broad group of industry advisors and stakeholders. It reflects their expectations about all aspects of sustainably sourced materials and is designed to be used by wide-ranging industry players.
Re-Source also has a direct link with the Battery Passport project of the Global Battery Alliance (GBA), through ERG, Umicore, Glencore and other Re-Source pilot partners, members of the GBA. The Battery Passport is aimed at transforming the entire value chain to make battery production more responsible and sustainable. The member companies believe that these projects support each other and together will deliver on the overarching agenda of increasing sustainability in the wider battery supply chain.
Marc Grynberg, CEO of Umicore, said: “I am proud to support Re-Source in developing a technology solution to assure traceability in the entire battery industry. For many years, Umicore has been a pioneer in promoting a sustainable value chain by only offering battery materials of a certified and ethical origin. Today, we share our expertise within this innovatory consortium and participate in the pilot to develop an industry-wide traceability technology, which is an important step towards a sustainable value chain for all batteries.”
Ivan Glasenberg, CEO of Glencore, said: “Blockchain technology offers us an unprecedented ability for traceability in the supply chain. Through this pilot, we are supporting the development of this tool for our customers who seek to understand and demonstrate the origin of the cobalt units in their products. But traceability is not enough on its own, it must be part of a wider industry effort to bring improvements to the entire cobalt supply chain. This starts with responsible sourcing compliance, for example through RMI; the collective use of wider ESG standards such as CIRAF and ICMM; and supporting the artisanal and small-scale mining (ASM) sector in the Democratic Republic of Congo (DRC) sector through multi-stakeholder initiatives like the Fair Cobalt Alliance (FCA).”
Sun Ruiwen, CEO of CMOC, said: “Re-Source is a very exciting development in global battery industry. As a global leading producer and trader of cobalt, CMOC and its trading affiliate IXM are committed to the responsible mining, processing and use of cobalt. We believe this initiative will help increase the transparency throughout the value chain. In the backdrop of the global energy transition and China pledging carbon neutrality by 2060, the battery industry is growing and expanding rapidly. A transparent and responsible supply chain, bringing together all stakeholders with this joint effort, will give end users greater confidence in cobalt as a raw material.”
Benedikt Sobotka, CEO of ERG and co-chair of the Global Battery Alliance, said: “Eurasian Resources Group prides itself on being a leading cobalt producer globally, operating the second-largest standalone cobalt production facility with a design capacity of 24 ktpa. As part of our continued efforts to ensure cobalt is responsibly sourced and processed, a key focus for ERG has been collaborating with leading public and private organisations to respond to the growing battery market powering the energy transition and the low carbon economy which is the biggest purchase order in history. Piloting the Re-Source solution is a vital milestone that brings us one step closer to unveiling the significant potential of batteries, while strengthening transparency and sustainability of battery materials across the value chain – also a mission of the Global Battery Alliance, where ERG is a founding member.”
A Blockchain Solution for Cobalt Traceability
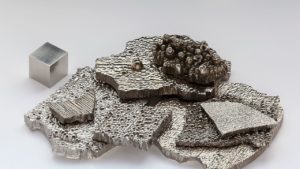
A global EV pioneer and one of the world’s leading battery makers are also part of the pilot. Tested in real operating conditions, from upstream cobalt production sites in the Democratic Republic of the Congo (DRC) to downstream electric vehicle production sites, the pilot will run until the end of 2021, with the roll-out of the final solution expected in 2022.
Assured through blockchain technology, the solution is a unique industry partnership between EV supply chain majors aiming to accelerate sustainable practices for every unit of cobalt mined, processed and used in end products. Founded by CMOC, ERG and Glencore and launched in 2019, Re-Source was later joined by Umicore, as well as a battery and EV company. It is designed with the direct input of responsible sourcing, and supply chain experts from all participating companies, proactively addressing the growing need for cobalt value chain visibility.
The collaboration between major cobalt industry players working in the DRC, deploys various technologies, including blockchain and Zero-Knowledge Proofs, to link digital flows with physical material flows on the ground. The ground-breaking solution is supported by boutique technology studio Kryha, which is experienced in carbon footprint and metals traceability and known for projects with the World Economic Forum.
To meet the consortiums’ mission of ensuring that all cobalt used in end products will be sustainably sourced, Re-Source integrates a comprehensive set of industrial sustainable mining and sourcing standards and frameworks, such as ICMM, RMI, IRMA CIRAF1, Copper Mark and others. The solution is therefore also exploring how aspects of the related GHG emissions along the value chain can be traced and disclosed.
In addition to EV supply chain majors, Re-Source is developed with the involvement of a broad group of industry advisors and stakeholders. It reflects their expectations about all aspects of sustainably sourced materials and is designed to be used by wide-ranging industry players.
Re-Source also has a direct link with the Battery Passport project of the Global Battery Alliance (GBA), through ERG, Umicore, Glencore and other Re-Source pilot partners, members of the GBA. The Battery Passport is aimed at transforming the entire value chain to make battery production more responsible and sustainable. The member companies believe that these projects support each other and together will deliver on the overarching agenda of increasing sustainability in the wider battery supply chain.
Marc Grynberg, CEO of Umicore, said: “I am proud to support Re-Source in developing a technology solution to assure traceability in the entire battery industry. For many years, Umicore has been a pioneer in promoting a sustainable value chain by only offering battery materials of a certified and ethical origin. Today, we share our expertise within this innovatory consortium and participate in the pilot to develop an industry-wide traceability technology, which is an important step towards a sustainable value chain for all batteries.”
Ivan Glasenberg, CEO of Glencore, said: “Blockchain technology offers us an unprecedented ability for traceability in the supply chain. Through this pilot, we are supporting the development of this tool for our customers who seek to understand and demonstrate the origin of the cobalt units in their products. But traceability is not enough on its own, it must be part of a wider industry effort to bring improvements to the entire cobalt supply chain. This starts with responsible sourcing compliance, for example through RMI; the collective use of wider ESG standards such as CIRAF and ICMM; and supporting the artisanal and small-scale mining (ASM) sector in the Democratic Republic of Congo (DRC) sector through multi-stakeholder initiatives like the Fair Cobalt Alliance (FCA).”
Sun Ruiwen, CEO of CMOC, said: “Re-Source is a very exciting development in global battery industry. As a global leading producer and trader of cobalt, CMOC and its trading affiliate IXM are committed to the responsible mining, processing and use of cobalt. We believe this initiative will help increase the transparency throughout the value chain. In the backdrop of the global energy transition and China pledging carbon neutrality by 2060, the battery industry is growing and expanding rapidly. A transparent and responsible supply chain, bringing together all stakeholders with this joint effort, will give end users greater confidence in cobalt as a raw material.”
Benedikt Sobotka, CEO of ERG and co-chair of the Global Battery Alliance, said: “Eurasian Resources Group prides itself on being a leading cobalt producer globally, operating the second-largest standalone cobalt production facility with a design capacity of 24 ktpa. As part of our continued efforts to ensure cobalt is responsibly sourced and processed, a key focus for ERG has been collaborating with leading public and private organisations to respond to the growing battery market powering the energy transition and the low carbon economy which is the biggest purchase order in history. Piloting the Re-Source solution is a vital milestone that brings us one step closer to unveiling the significant potential of batteries, while strengthening transparency and sustainability of battery materials across the value chain – also a mission of the Global Battery Alliance, where ERG is a founding member.”
Tomra Recycling invites to webinar on aluminum recycling
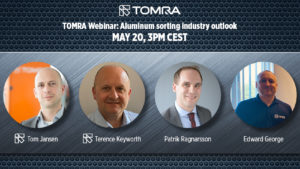
The aluminum recycling industry is constantly evolving and adapting to an increasing demand for this highly versatile material which results, among others, from a rise in electronic vehicle production, the trend towards more lightweight cars and the outstanding features this non-ferrous metal brings to numerous industries. A rise in demand offers a valuable proposition for the industry as it strongly encourages a more sustainable production which, in turn, supports the industry on its progress towards greener aluminum production.
Tomra’s webinar will further explore the future of the global aluminum recycling industry and detail how recycling can build the bridge between market pull and the industry push for greener aluminum.
In the 45 minutes live session, attendees can look forward to learning more about the aluminum recycling industry in general and recent innovations in sensor-based sorting technology, which will be highlighted by Tomra’s Segment Managers Metal Recycling, Tom Jansen and Terence Keyworth. In addition, Patrik Ragnarsson, Senior Manager Automotive and Transport at European Aluminium, will address the general trends in the automotive sector, especially with regards to the increase in electronic vehicle production, and will also detail the role aluminium plays within the sector. First-hand experiences in the scrap recycling landscape and the importance of having advanced technologies in place will be highlighted by Edward George, Commercial Manager at Alutrade Ltd.
A closing and interactive Q&A session at the end of the webinar which will provide an opportunity to explore specific topics in more detail.
Tomra Recycling invites to webinar on aluminum recycling
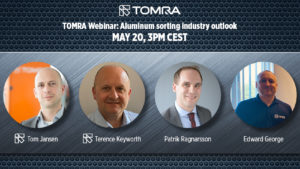
The aluminum recycling industry is constantly evolving and adapting to an increasing demand for this highly versatile material which results, among others, from a rise in electronic vehicle production, the trend towards more lightweight cars and the outstanding features this non-ferrous metal brings to numerous industries. A rise in demand offers a valuable proposition for the industry as it strongly encourages a more sustainable production which, in turn, supports the industry on its progress towards greener aluminum production.
Tomra’s webinar will further explore the future of the global aluminum recycling industry and detail how recycling can build the bridge between market pull and the industry push for greener aluminum.
In the 45 minutes live session, attendees can look forward to learning more about the aluminum recycling industry in general and recent innovations in sensor-based sorting technology, which will be highlighted by Tomra’s Segment Managers Metal Recycling, Tom Jansen and Terence Keyworth. In addition, Patrik Ragnarsson, Senior Manager Automotive and Transport at European Aluminium, will address the general trends in the automotive sector, especially with regards to the increase in electronic vehicle production, and will also detail the role aluminium plays within the sector. First-hand experiences in the scrap recycling landscape and the importance of having advanced technologies in place will be highlighted by Edward George, Commercial Manager at Alutrade Ltd.
A closing and interactive Q&A session at the end of the webinar which will provide an opportunity to explore specific topics in more detail.
Greater operational reliability in scrap and aluminium recycling
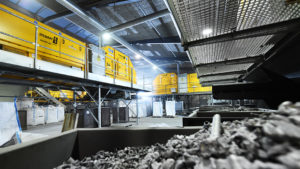
In situations, for example, where recovered, recycled aluminium is being used to produce new products, aluminium manufacturers need their secondary raw materials to display consistently high levels of purity. This is one of the challenges solved by sorting technology. Dry density sorting using x-ray transmission is a proven method that is used by hundreds of metal recycling firms around the globe. Simply considering processors of the high-performance material aluminium, the sorting machine is used to separate free heavy metals, aluminium compounds, free magnesium and wrought and cast aluminium parts. Steinert’s ongoing development work now ensures specific benefits for the sorting process.
EVO 5.0 generation with new functions
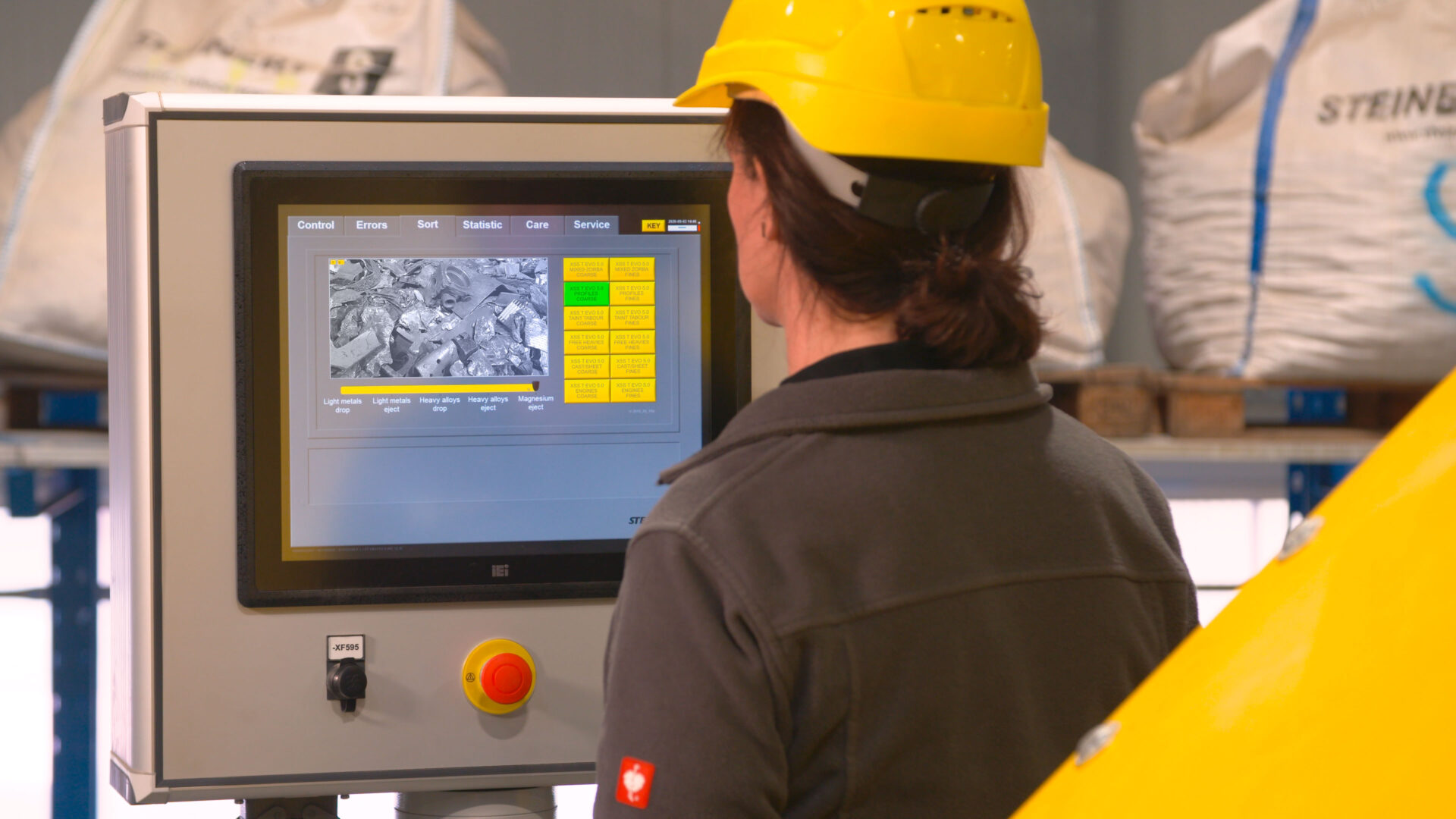
Thanks to Multilayer Data Evaluation (MDE), the sorting machine is able to use even more distinguishing criteria for detection thanks to high-resolution object recognition and by undertaking classification in parallel. Complex sorting tasks, such as magnesium detection are solved easily. Automatic x-ray monitoring and calibration (AXM) of the x-ray sensors help achieve consistently high detection and sorting quality.
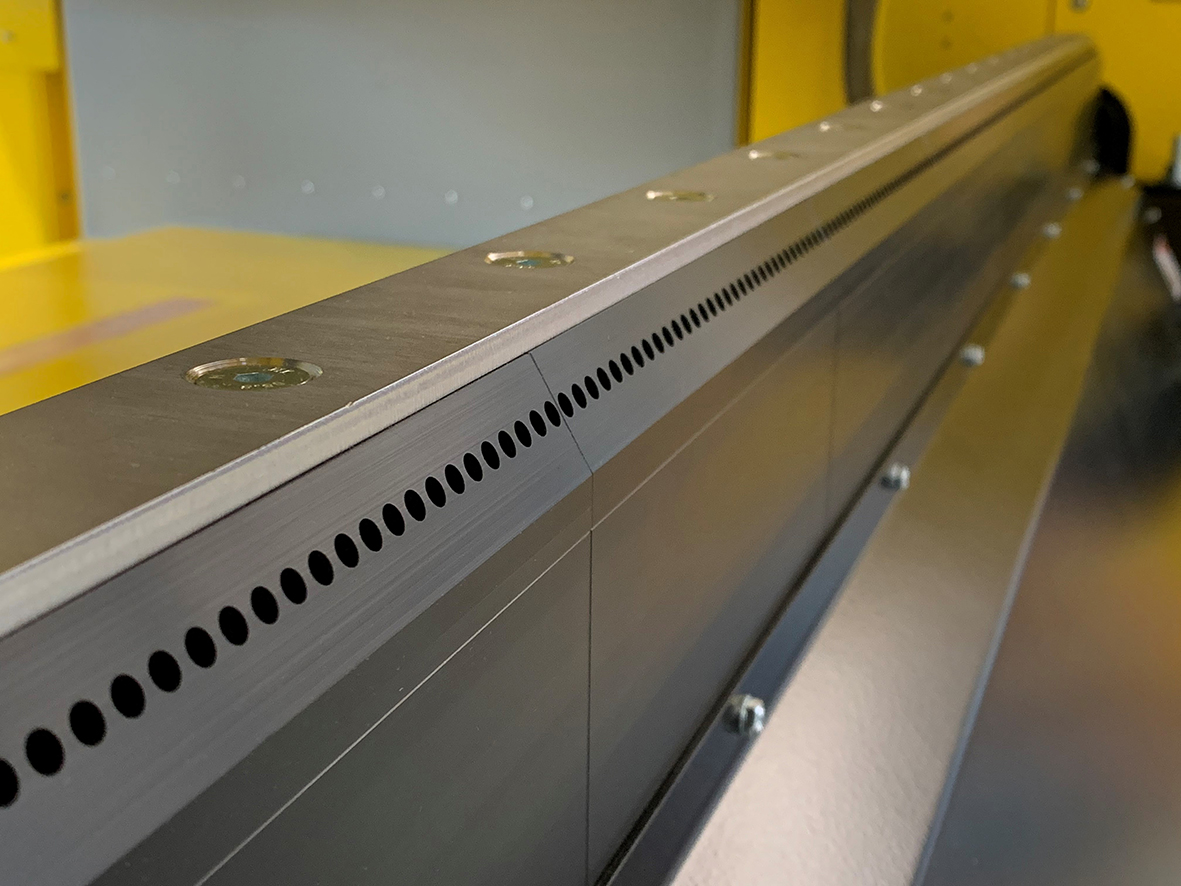
The hardware has also been improved. The high-resolution valve pitch of 6.25 mm enables even more efficient sorting of fine material down to 5 mm. The x-ray scan area is cleaned automatically in the new generation of machines. This vastly reduces the amount of manual cleaning needed and maintains a consistently high level of detection quality. The 4-year warranty for the x-ray source and sensors provides operational reliability and keeps operating costs low.
A so-called solution guide can be downloaded as an e-book to provide an initial overview of the opportunities provided for sorting aluminium scrap and other materials. Although aluminium scrap comes from different sources like profiles and plates, incineration bottom ash, shredder systems or Dense Media Separation (DMS), the rough stages of the sorting process are similar: recovering non-ferrous metals and upgrading the recovered metals, in other words, producing pure metal types. The e-book provides insight into both the heart of the systems – the Steinert XSS T EVO 5.0 – as well as the upstream magnet technology and downstream fluorescence technology; of benefit to operators of aluminium shredders, secondary smelters or processors of waste incinerator ash. The downstream fluorescence technology produces pure heavy metal fractions such as copper, brass and zinc.
Greater operational reliability in scrap and aluminium recycling
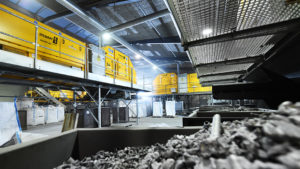
In situations, for example, where recovered, recycled aluminium is being used to produce new products, aluminium manufacturers need their secondary raw materials to display consistently high levels of purity. This is one of the challenges solved by sorting technology. Dry density sorting using x-ray transmission is a proven method that is used by hundreds of metal recycling firms around the globe. Simply considering processors of the high-performance material aluminium, the sorting machine is used to separate free heavy metals, aluminium compounds, free magnesium and wrought and cast aluminium parts. Steinert’s ongoing development work now ensures specific benefits for the sorting process.
EVO 5.0 generation with new functions
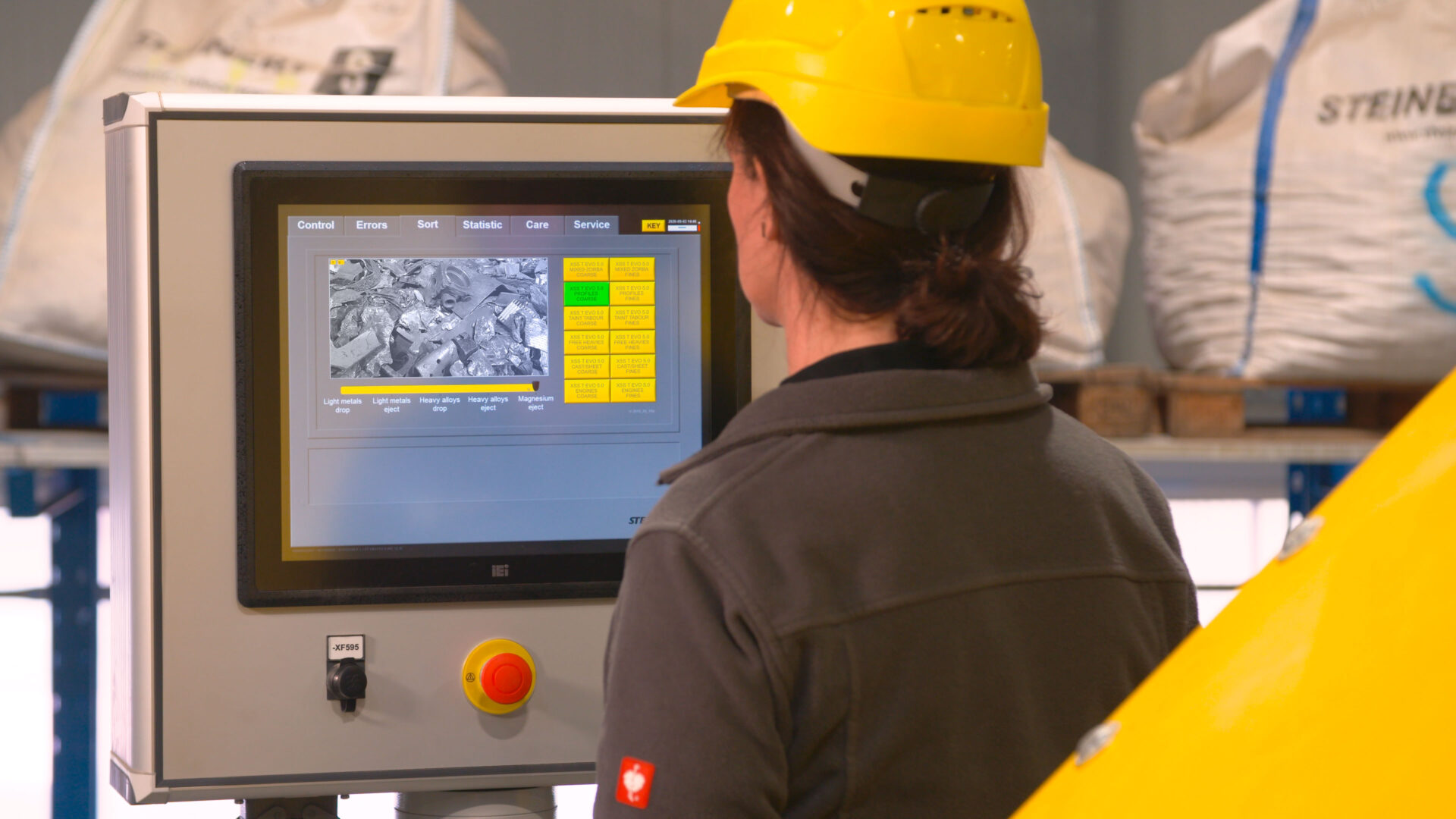
Thanks to Multilayer Data Evaluation (MDE), the sorting machine is able to use even more distinguishing criteria for detection thanks to high-resolution object recognition and by undertaking classification in parallel. Complex sorting tasks, such as magnesium detection are solved easily. Automatic x-ray monitoring and calibration (AXM) of the x-ray sensors help achieve consistently high detection and sorting quality.
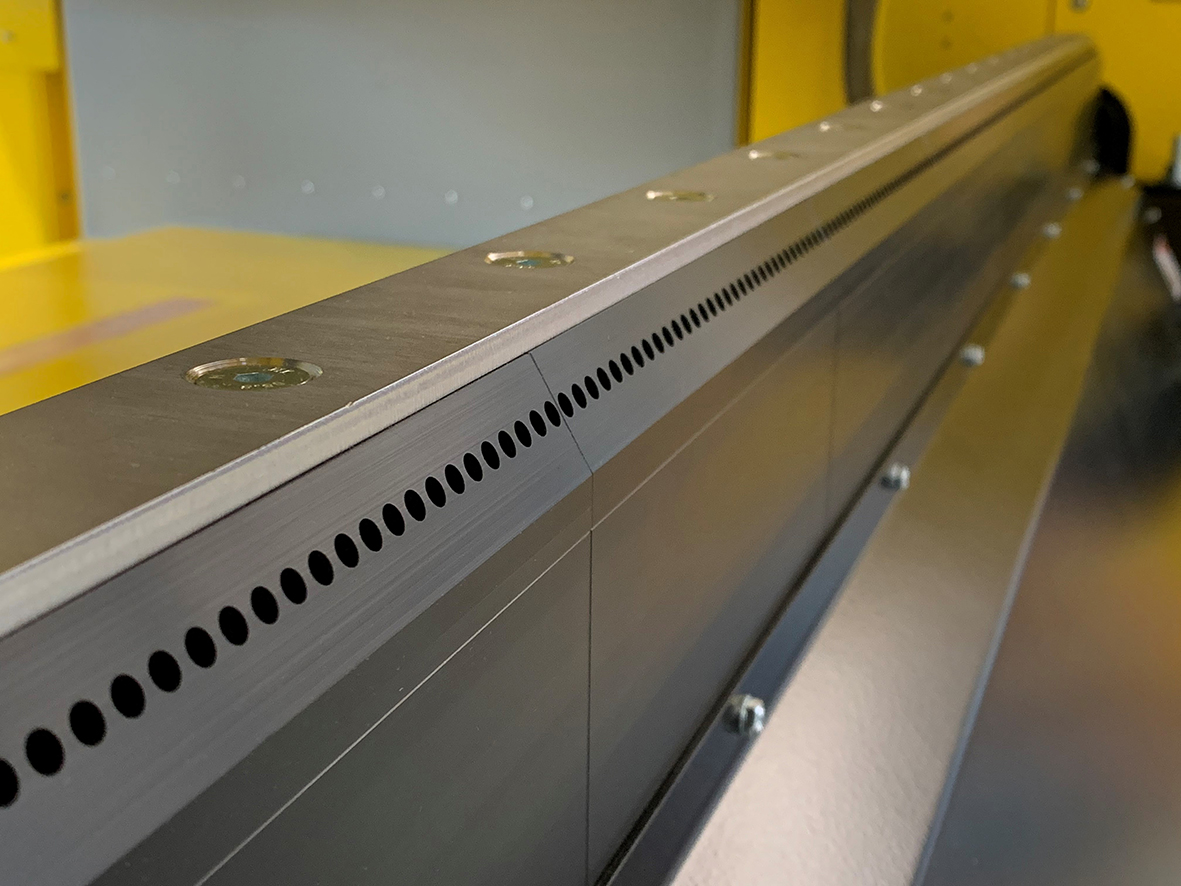
The hardware has also been improved. The high-resolution valve pitch of 6.25 mm enables even more efficient sorting of fine material down to 5 mm. The x-ray scan area is cleaned automatically in the new generation of machines. This vastly reduces the amount of manual cleaning needed and maintains a consistently high level of detection quality. The 4-year warranty for the x-ray source and sensors provides operational reliability and keeps operating costs low.
A so-called solution guide can be downloaded as an e-book to provide an initial overview of the opportunities provided for sorting aluminium scrap and other materials. Although aluminium scrap comes from different sources like profiles and plates, incineration bottom ash, shredder systems or Dense Media Separation (DMS), the rough stages of the sorting process are similar: recovering non-ferrous metals and upgrading the recovered metals, in other words, producing pure metal types. The e-book provides insight into both the heart of the systems – the Steinert XSS T EVO 5.0 – as well as the upstream magnet technology and downstream fluorescence technology; of benefit to operators of aluminium shredders, secondary smelters or processors of waste incinerator ash. The downstream fluorescence technology produces pure heavy metal fractions such as copper, brass and zinc.
Greater operational reliability in scrap and aluminium recycling
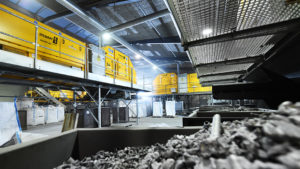
In situations, for example, where recovered, recycled aluminium is being used to produce new products, aluminium manufacturers need their secondary raw materials to display consistently high levels of purity. This is one of the challenges solved by sorting technology. Dry density sorting using x-ray transmission is a proven method that is used by hundreds of metal recycling firms around the globe. Simply considering processors of the high-performance material aluminium, the sorting machine is used to separate free heavy metals, aluminium compounds, free magnesium and wrought and cast aluminium parts. Steinert’s ongoing development work now ensures specific benefits for the sorting process.
EVO 5.0 generation with new functions
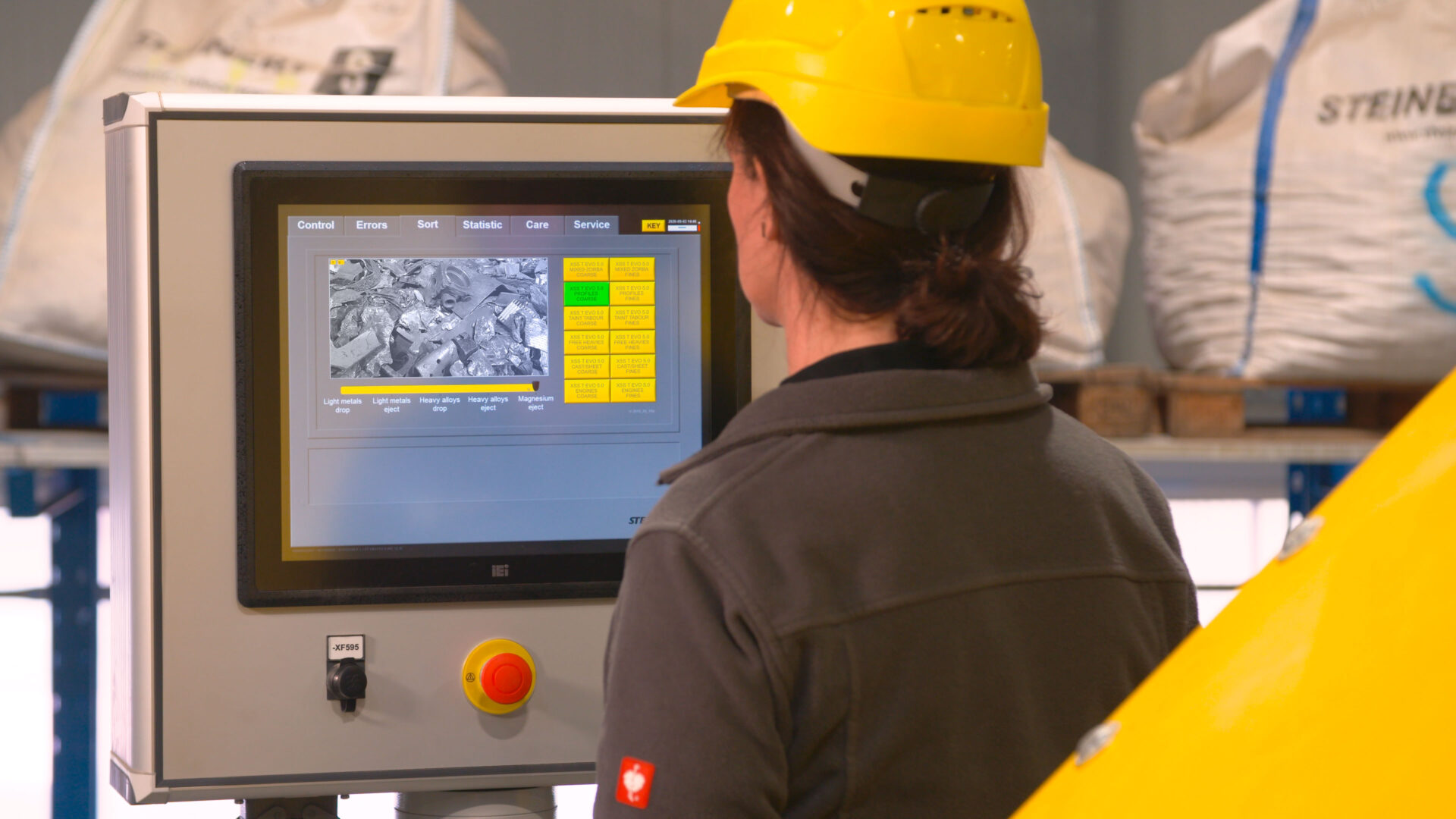
Thanks to Multilayer Data Evaluation (MDE), the sorting machine is able to use even more distinguishing criteria for detection thanks to high-resolution object recognition and by undertaking classification in parallel. Complex sorting tasks, such as magnesium detection are solved easily. Automatic x-ray monitoring and calibration (AXM) of the x-ray sensors help achieve consistently high detection and sorting quality.
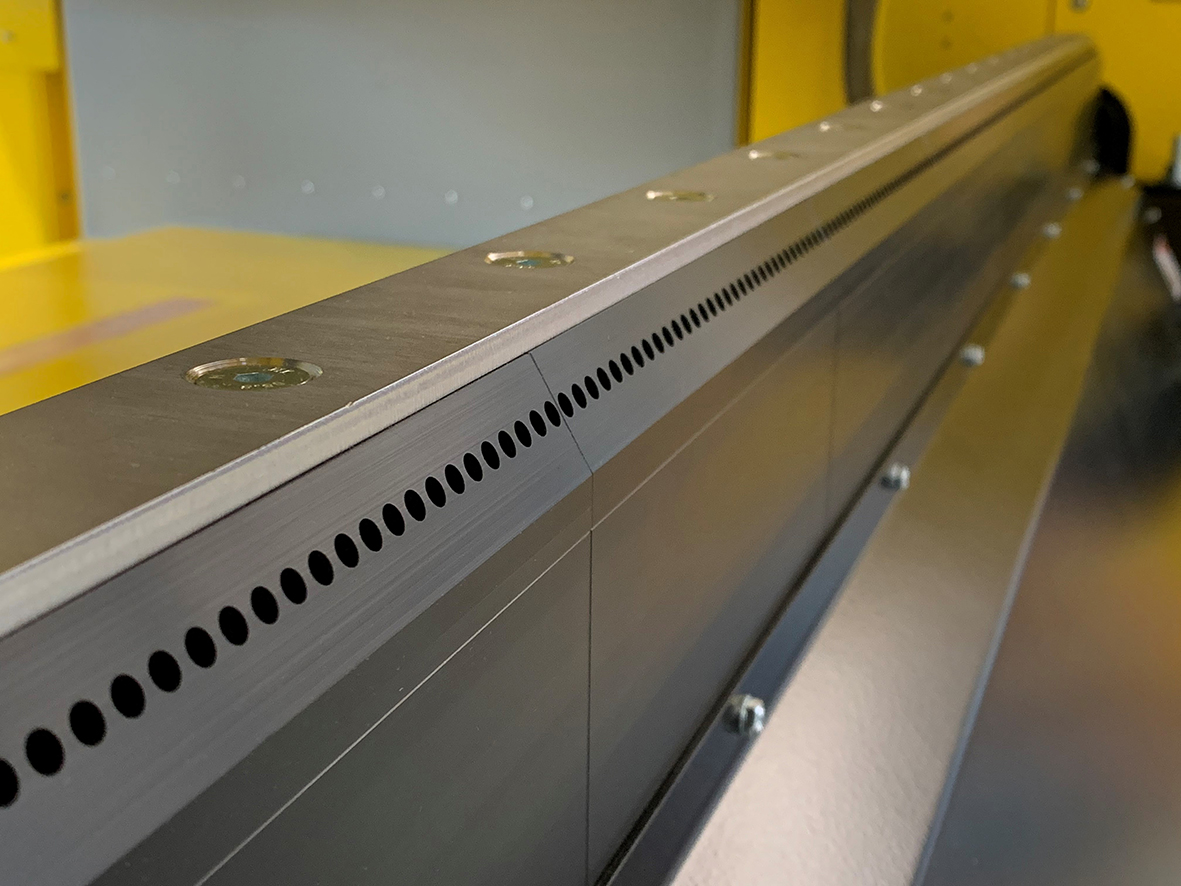
The hardware has also been improved. The high-resolution valve pitch of 6.25 mm enables even more efficient sorting of fine material down to 5 mm. The x-ray scan area is cleaned automatically in the new generation of machines. This vastly reduces the amount of manual cleaning needed and maintains a consistently high level of detection quality. The 4-year warranty for the x-ray source and sensors provides operational reliability and keeps operating costs low.
A so-called solution guide can be downloaded as an e-book to provide an initial overview of the opportunities provided for sorting aluminium scrap and other materials. Although aluminium scrap comes from different sources like profiles and plates, incineration bottom ash, shredder systems or Dense Media Separation (DMS), the rough stages of the sorting process are similar: recovering non-ferrous metals and upgrading the recovered metals, in other words, producing pure metal types. The e-book provides insight into both the heart of the systems – the Steinert XSS T EVO 5.0 – as well as the upstream magnet technology and downstream fluorescence technology; of benefit to operators of aluminium shredders, secondary smelters or processors of waste incinerator ash. The downstream fluorescence technology produces pure heavy metal fractions such as copper, brass and zinc.
Greater operational reliability in scrap and aluminium recycling
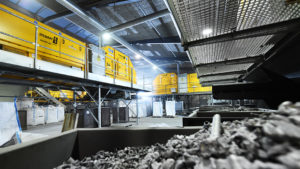
In situations, for example, where recovered, recycled aluminium is being used to produce new products, aluminium manufacturers need their secondary raw materials to display consistently high levels of purity. This is one of the challenges solved by sorting technology. Dry density sorting using x-ray transmission is a proven method that is used by hundreds of metal recycling firms around the globe. Simply considering processors of the high-performance material aluminium, the sorting machine is used to separate free heavy metals, aluminium compounds, free magnesium and wrought and cast aluminium parts. Steinert’s ongoing development work now ensures specific benefits for the sorting process.
EVO 5.0 generation with new functions
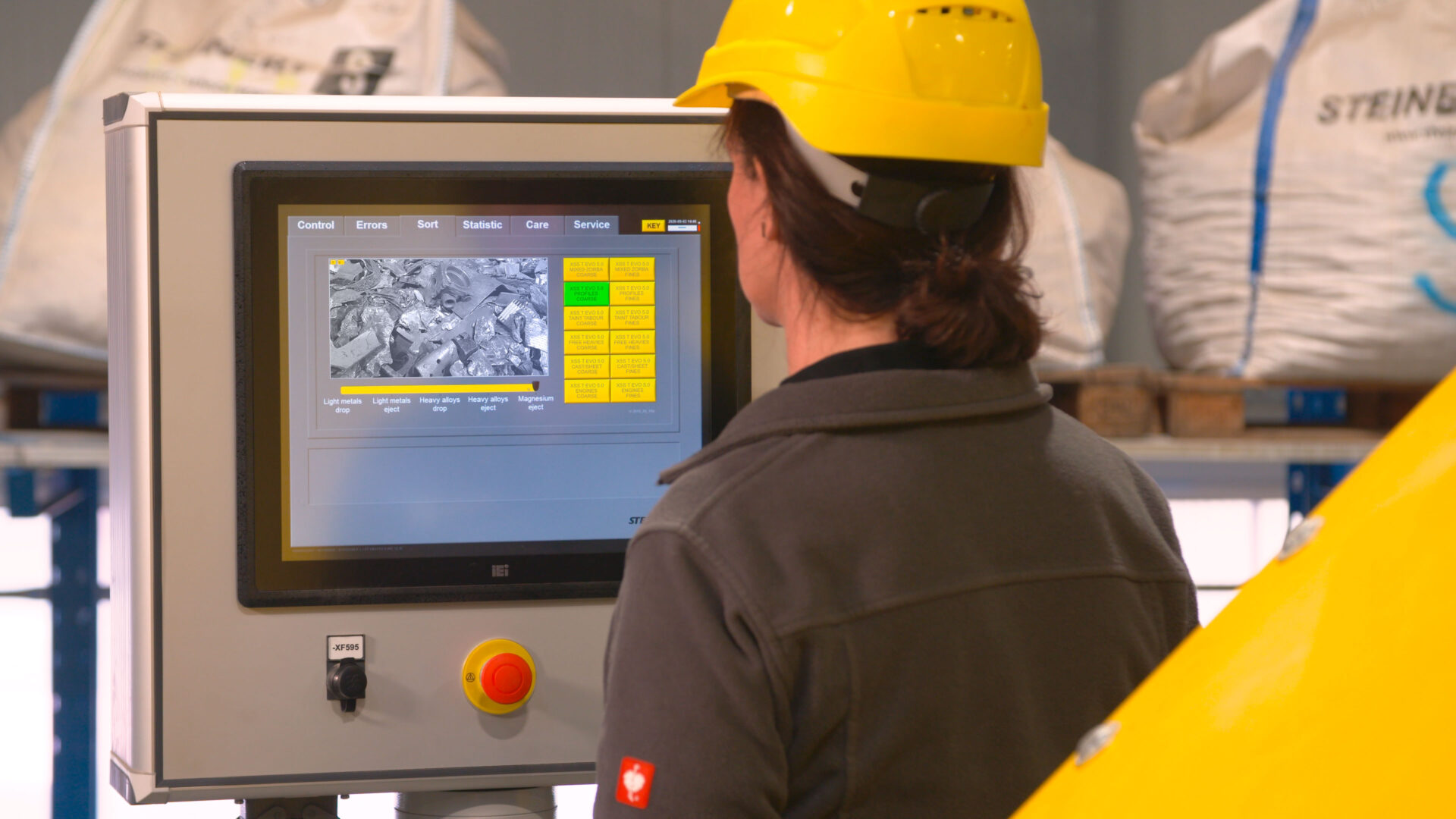
Thanks to Multilayer Data Evaluation (MDE), the sorting machine is able to use even more distinguishing criteria for detection thanks to high-resolution object recognition and by undertaking classification in parallel. Complex sorting tasks, such as magnesium detection are solved easily. Automatic x-ray monitoring and calibration (AXM) of the x-ray sensors help achieve consistently high detection and sorting quality.
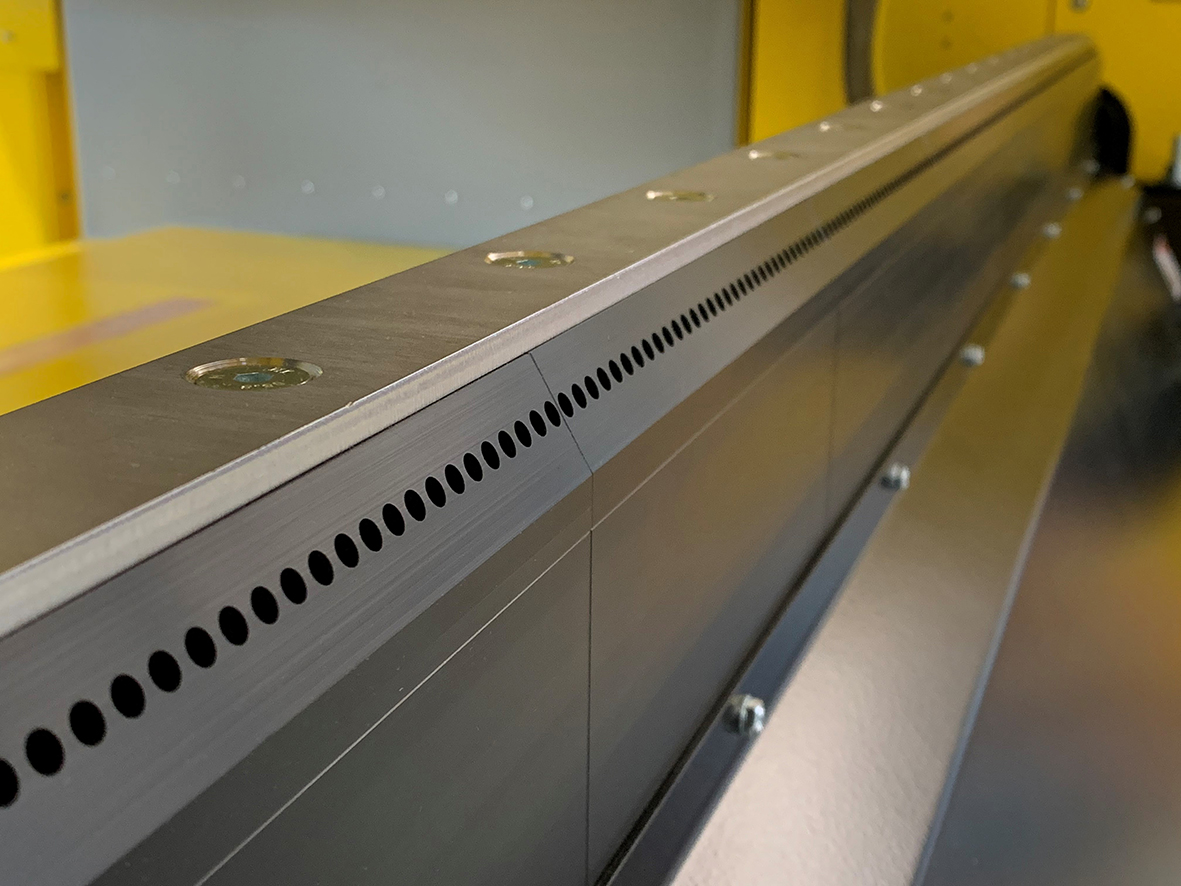
The hardware has also been improved. The high-resolution valve pitch of 6.25 mm enables even more efficient sorting of fine material down to 5 mm. The x-ray scan area is cleaned automatically in the new generation of machines. This vastly reduces the amount of manual cleaning needed and maintains a consistently high level of detection quality. The 4-year warranty for the x-ray source and sensors provides operational reliability and keeps operating costs low.
A so-called solution guide can be downloaded as an e-book to provide an initial overview of the opportunities provided for sorting aluminium scrap and other materials. Although aluminium scrap comes from different sources like profiles and plates, incineration bottom ash, shredder systems or Dense Media Separation (DMS), the rough stages of the sorting process are similar: recovering non-ferrous metals and upgrading the recovered metals, in other words, producing pure metal types. The e-book provides insight into both the heart of the systems – the Steinert XSS T EVO 5.0 – as well as the upstream magnet technology and downstream fluorescence technology; of benefit to operators of aluminium shredders, secondary smelters or processors of waste incinerator ash. The downstream fluorescence technology produces pure heavy metal fractions such as copper, brass and zinc.
Global Recycling Foundations Reforestation Initiative
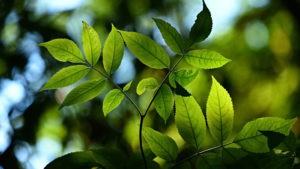
The event, held in conjunction with the Global Recycling Foundation (GRF), also marked 20 years in business by Recycled Products. The company was honored to have the founding president of the GRF, Ranjit Baxi, join with managing director Susie Burrage in planting the first tree – a Prunus Cherry Plum, which had just started to blossom. The other trees include beech, which have come to symbolise the idyllic Chilterns countryside.
Recycled Products is leading the way in backing the UK’s goal to be net carbon neutral by 2050. By using recycled copper, CO2 emissions can be reduced by 65% compared to use of mined primary copper, for example. Recycling aluminium gives a higher 92% reduction, and the figure is a headline, 99% for recycled lead.
Susie Burrage, managing director of Recycled Products, said: “All recycled materials are inherently low carbon, so metal recyclers have a key role to play as society looks to cut CO2 emissions in the decades ahead. This doesn’t absolve us of all responsibility for working on reducing our own carbon footprint, however.
“Global Recycling Day is a great reminder that we all – from individuals to large companies and governments – must play our part in achieving net-zero carbon emissions and limit the worst effects of climate change.
“Those of us working in the recycling sector are more aware of this than most and are therefore making every effort to limit our carbon emissions. Recycled Products are offsetting unavoidable emissions by planting trees.”