Science & technology
Recyclable PVC to remain polymer of choice for medical devices
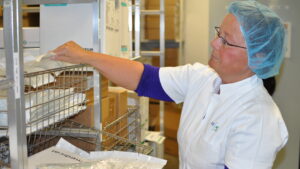
The high volume and PVC’s unique recyclability indicate that hospitals should start with PVC in recycling schemes for plastics-based medical devices.
Almost 30% of the plastics-based medical devices are manufactured in PVC, which makes the material the most used polymer for bags, tubing, masks and other disposable medical devices. The remaining share is divided between ten different polymers. This is one of the key findings in a new market study conducted by Global Market Insights Inc., a global market research and management consulting company. The study also forecasts that PVC will retain its number one position until at least 2027.
PVC is easily recyclable and so versatile that devices which require both soft and rigid parts can be made entirely of one polymer – a key to successful plastic recycling. The high volume and PVC’s unique recyclability indicate that hospitals should start with this plastic material when they consider recycling schemes for their medical plastic waste.
PVCMed Alliance Project Manager Ole Grøndahl Hansen comments on the new findings: “COVID-19 has highlighted the crucial role played by single-use plastic medical devices in the prevention and control of infection in hospitals. The negative side-effect of this success has been growing amounts of hospital plastic waste. We believe recycling is part of the solution. Fortunately, the most used plastic in healthcare is also the most recyclable plastic, and we therefore urge hospitals to start their recycling activities with PVC.”
The presence of CMR substances in some PVC devices has thus far been a barrier to recycling of medical PVC. According to Ole Grøndahl Hansen this challenge has now been solved: “For almost all applications, alternative plasticizers for PVC are available and are being used. Four of these are now included in the European Pharmacopeia, which sets the safety and quality guidelines for medical products in Europe and beyond.”
The European PVC industry, through VinylPlus, has invested in recycling of PVC medical devices since 2014 when the RecoMed take back scheme was established in the UK. The scheme was inspired by the successful PVC in hospitals recycling project in Australia and New Zealand, which involves over 250 hospitals.
In February 2021, VinylPlus launched a collaborative project called VinylPlus® Med. Aimed at accelerating sustainability in healthcare across Europe through the recycling of discarded single-use PVC medical devices, the project brings together hospitals, waste managers, recyclers and the PVC industry in some selected European countries.
The scheme will focus on the production of PVC recyclates free of substances of concerns that can be included into a wide range of value products marketed across Europe. Belgium is chosen as pilot country with The Europe Hospitals, Renewi (waste management company) and Raff Plastics (recycler) as partners. The built-up of additional programmes is underway in other European countries.
Recyclable PVC to remain polymer of choice for medical devices
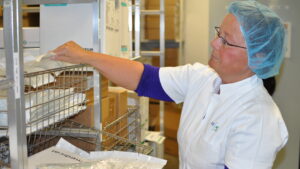
The high volume and PVC’s unique recyclability indicate that hospitals should start with PVC in recycling schemes for plastics-based medical devices.
Almost 30% of the plastics-based medical devices are manufactured in PVC, which makes the material the most used polymer for bags, tubing, masks and other disposable medical devices. The remaining share is divided between ten different polymers. This is one of the key findings in a new market study conducted by Global Market Insights Inc., a global market research and management consulting company. The study also forecasts that PVC will retain its number one position until at least 2027.
PVC is easily recyclable and so versatile that devices which require both soft and rigid parts can be made entirely of one polymer – a key to successful plastic recycling. The high volume and PVC’s unique recyclability indicate that hospitals should start with this plastic material when they consider recycling schemes for their medical plastic waste.
PVCMed Alliance Project Manager Ole Grøndahl Hansen comments on the new findings: “COVID-19 has highlighted the crucial role played by single-use plastic medical devices in the prevention and control of infection in hospitals. The negative side-effect of this success has been growing amounts of hospital plastic waste. We believe recycling is part of the solution. Fortunately, the most used plastic in healthcare is also the most recyclable plastic, and we therefore urge hospitals to start their recycling activities with PVC.”
The presence of CMR substances in some PVC devices has thus far been a barrier to recycling of medical PVC. According to Ole Grøndahl Hansen this challenge has now been solved: “For almost all applications, alternative plasticizers for PVC are available and are being used. Four of these are now included in the European Pharmacopeia, which sets the safety and quality guidelines for medical products in Europe and beyond.”
The European PVC industry, through VinylPlus, has invested in recycling of PVC medical devices since 2014 when the RecoMed take back scheme was established in the UK. The scheme was inspired by the successful PVC in hospitals recycling project in Australia and New Zealand, which involves over 250 hospitals.
In February 2021, VinylPlus launched a collaborative project called VinylPlus® Med. Aimed at accelerating sustainability in healthcare across Europe through the recycling of discarded single-use PVC medical devices, the project brings together hospitals, waste managers, recyclers and the PVC industry in some selected European countries.
The scheme will focus on the production of PVC recyclates free of substances of concerns that can be included into a wide range of value products marketed across Europe. Belgium is chosen as pilot country with The Europe Hospitals, Renewi (waste management company) and Raff Plastics (recycler) as partners. The built-up of additional programmes is underway in other European countries.
Green Alley Award 2022: Call for Applications are open
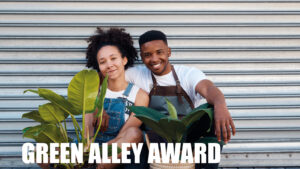
The Green Alley Award is Europe’s first startup prize for the circular economy, established in 2014 by Landbell Group. Founders and startups are invited to submit their application for the 2022 Green Alley Award online at green-alley-award.com. The best ideas will be selected for a live pitch in April 2022.
The 2022 Green Alley Award targets startups and young entrepreneurs who have developed a business model in the areas of digital circular economy, recycling and waste prevention. The award sponsors are looking for companies that are about to launch their products or services or are already in the growth phase. They also welcome startups who want to expand into other European markets. The sole condition is that the business idea must help reduce waste or turn waste into resources.
‘We want to encourage new ideas and business models to save resources and reduce waste,’ says Jan Patrick Schulz, CEO of Landbell Group. ‘There are so many creative ideas around. Our aim is to foster and promote young founders and connect them to our vast network of circular economy experts across Europe.’
The Winners – a wide range of concepts
Whether it is the development of sustainable materials, ideas for waste reduction or helpful digital tools, the circular economy holds enormous business potential for startups. The diversity of concepts from Green Alley Award winners over the past years clearly shows this, e.g. traceless materials from Germany, which won the 2021 award for a patent pending technology that transforms agricultural industry residues into a sustainable plastic alternative. In 2019, Estonian startup Gelatex Technologies convinced the jury with their unique idea of an alternative to conventional leather made of by-product gelatin. In 2017, the Finnish startup Sulapac presented a wooden, biodegradable alternative to plastic packaging for the cosmetic industry. The winner of the first Green Alley Award in 2014 was the Finnish startup RePack. It provides reusable packaging service for the e-commerce industry.
The Application Process
- Startups are invited to submit their application by 23rd November 2021.
- A pre-selected number of startups will be put on the Green Alley Award website for a public vote. The startup with the majority of the votes will be automatically amongst the six finalists. The remaining five will be selected by our expert committee.
- On 28th April 2022 the six finalists will be invited to Berlin, where they will meet circular economy and startup experts in working sessions. In the evening each of the finalists will have the chance to pitch their idea live on stage to an expert jury and international audience.
Green Alley Award 2022: Call for Applications are open
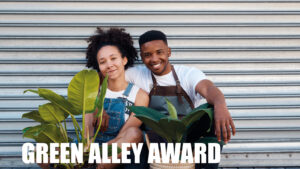
The Green Alley Award is Europe’s first startup prize for the circular economy, established in 2014 by Landbell Group. Founders and startups are invited to submit their application for the 2022 Green Alley Award online at green-alley-award.com. The best ideas will be selected for a live pitch in April 2022.
The 2022 Green Alley Award targets startups and young entrepreneurs who have developed a business model in the areas of digital circular economy, recycling and waste prevention. The award sponsors are looking for companies that are about to launch their products or services or are already in the growth phase. They also welcome startups who want to expand into other European markets. The sole condition is that the business idea must help reduce waste or turn waste into resources.
‘We want to encourage new ideas and business models to save resources and reduce waste,’ says Jan Patrick Schulz, CEO of Landbell Group. ‘There are so many creative ideas around. Our aim is to foster and promote young founders and connect them to our vast network of circular economy experts across Europe.’
The Winners – a wide range of concepts
Whether it is the development of sustainable materials, ideas for waste reduction or helpful digital tools, the circular economy holds enormous business potential for startups. The diversity of concepts from Green Alley Award winners over the past years clearly shows this, e.g. traceless materials from Germany, which won the 2021 award for a patent pending technology that transforms agricultural industry residues into a sustainable plastic alternative. In 2019, Estonian startup Gelatex Technologies convinced the jury with their unique idea of an alternative to conventional leather made of by-product gelatin. In 2017, the Finnish startup Sulapac presented a wooden, biodegradable alternative to plastic packaging for the cosmetic industry. The winner of the first Green Alley Award in 2014 was the Finnish startup RePack. It provides reusable packaging service for the e-commerce industry.
The Application Process
- Startups are invited to submit their application by 23rd November 2021.
- A pre-selected number of startups will be put on the Green Alley Award website for a public vote. The startup with the majority of the votes will be automatically amongst the six finalists. The remaining five will be selected by our expert committee.
- On 28th April 2022 the six finalists will be invited to Berlin, where they will meet circular economy and startup experts in working sessions. In the evening each of the finalists will have the chance to pitch their idea live on stage to an expert jury and international audience.
Breaking new ground in Turkey’s textile industry
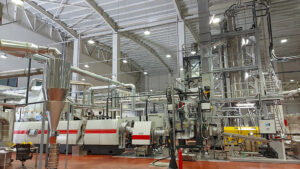
The Starlinger recoSTAR universal 165 H-VAC iV+, which is part of Korteks’ 10 million dollars investment in a new polymer recycling facility, took up operation in May 2021. It has a production capacity of 7,200 tons per year and currently processes clean in-house polyester fibers from production scrap together with washed post-consumer PET flakes at a ratio of 50/50. Korteks uses the polyester regranulate at a share of 100 % for its new polyester filament yarn line it is going to market under the name “TAÇ Reborn”. With this investment, the company has made an important step towards establishing a circular economy in the Turkish textile industry.
“We have been in extensive cooperation with Starlinger for a long time” said Barış Mert, General Manager of Korteks. “Thanks to their unique and innovative recycling technology we can offer new products in line with the circular economy model. That’s why, as Europe’s largest integrated and innovative polyester yarn producer, we are very pleased to work with Starlinger, the market leader in PET and polyester recycling and refining.”
Rapid Sleeve Changer: Finest melt filtration for perfect yarn
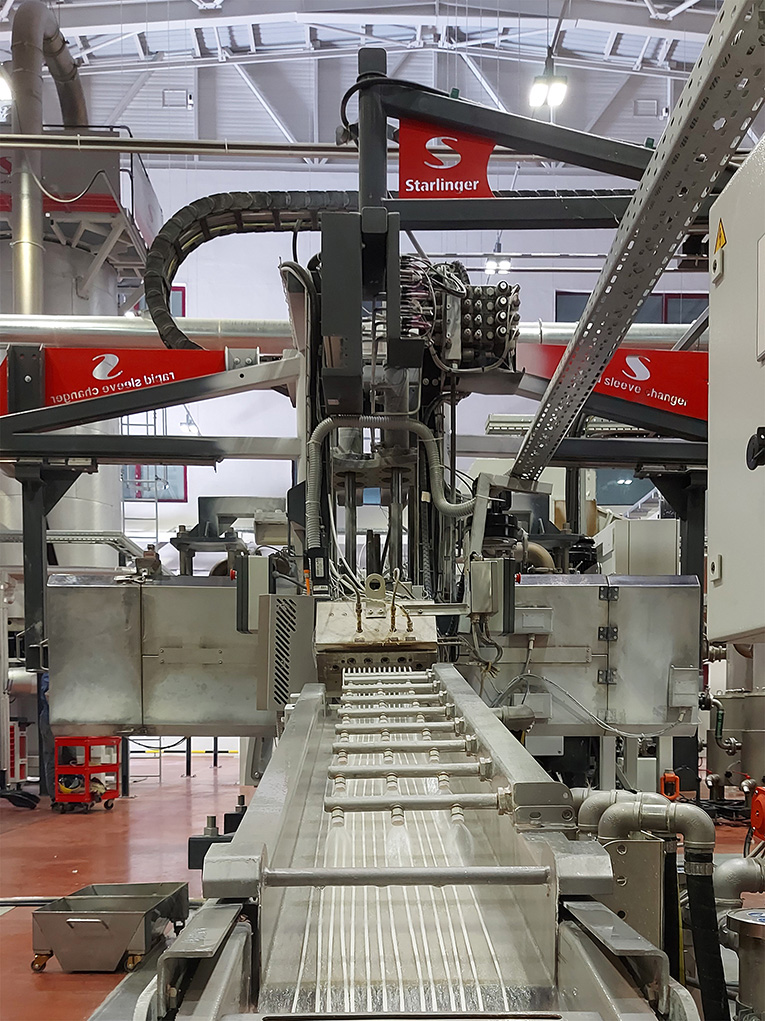
The Starlinger recycling line is the first of its kind in Turkey and is equipped with special components for filament yarn recycling. A RSC (Rapid Sleeve Changer) candle filter developed by Starlinger ensures finest melt filtration down to 15 μm. It has been specially designed for polyester recycling and reaches an output of 1000 kg/h. For continuous operation the filter elements are changed “on the fly” without interrupting production, which significantly limits melt loss.
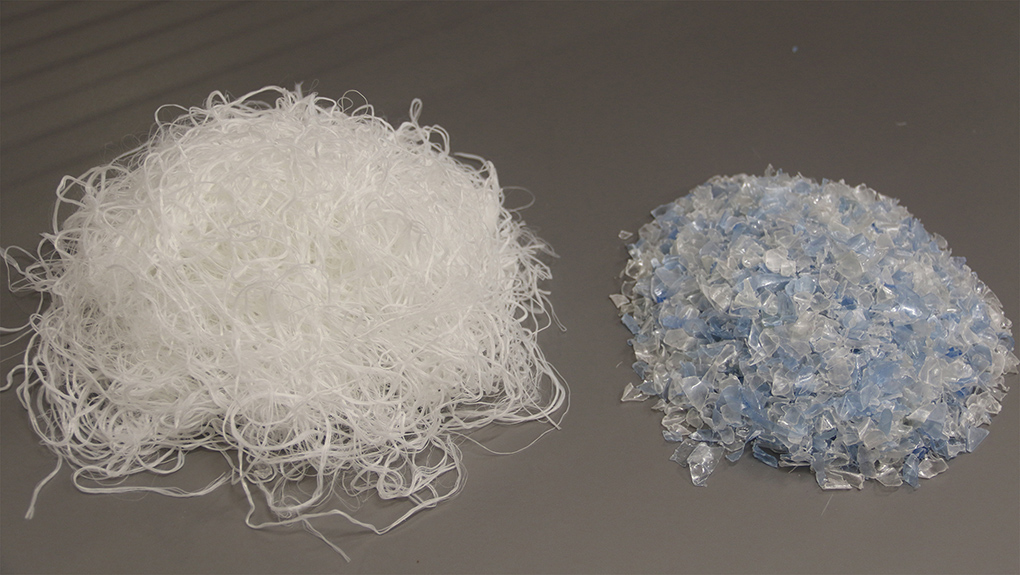
The viscoSTAR SSP unit at the end of the recycling process guarantees consistent IV increase according to the first-in-first-out principle. This makes sure that the produced regranulate has the ideal properties required for filament yarn production. The technical configuration of the line does not only allow the processing of a polyester fiber/PET flake mix as input materials, but also 100 % polyester filament scrap or 100 % PET bottle flakes.
With the new recycling facility, which comprises a total closed area of 17,000 m² and has a monthly production capacity of 600 tons, Korteks was able to reduce the production waste at its virgin PES yarn site to zero.
A paradigm shift in synthetic fiber production
“We are proud to be a partner in Korteks’ quest for more sustainability in the textile business”, said Paul Niedl, Commercial Head of Starlinger recycling technology. “Turkey is a significant global player in this industry. If more and more Turkish textile manufacturers start using recycled materials, this will be an important signal for the sector and a big step towards a circular economy. We support this development with our extensive know-how in synthetic fiber recycling and supply the fine-tuned and reliable recycling technology required in this field.”
Korteks expects the recycling market in general to grow as there is increased acceptance for recycled products in the society, and predicts the need for recycling solutions also for other synthetic and natural fibers.
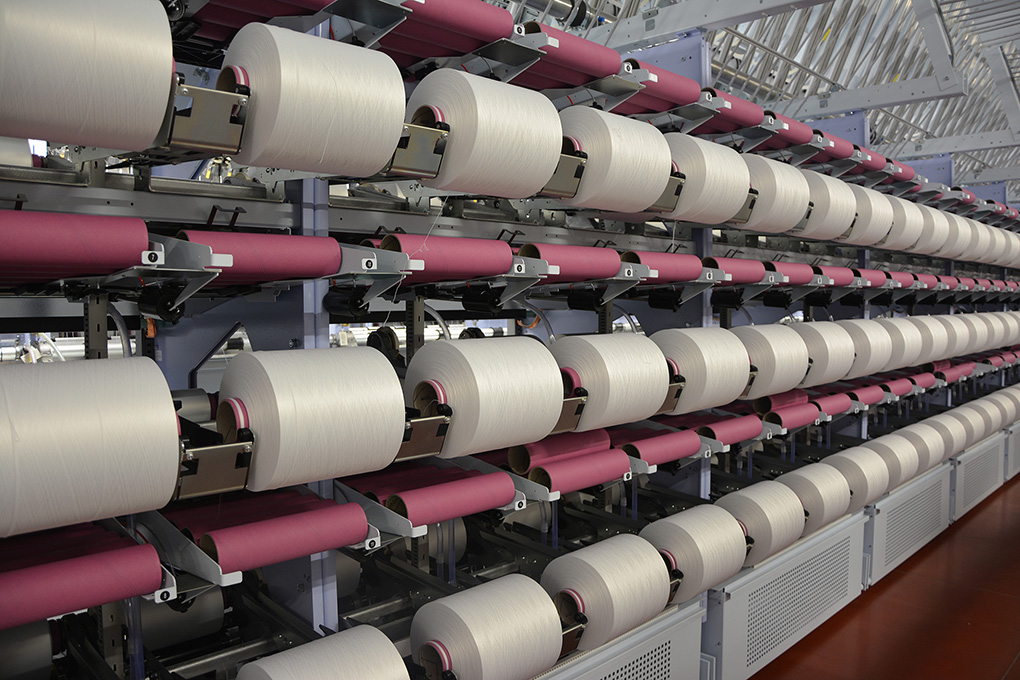
“At Korteks, we always aim at sustainable growth that reduces environmental impact and creates value. For this reason, we are gradually expanding our product range in sustainable and smart textiles every day”, said Barış Mert. “The period of the pandemic that the world has been going through has once again strikingly revealed the necessity of building a sustainable living together. The textile industry is also deeply affected by this big transformation on the globe. We believe that those who can manage this change well will also set the global textile agenda in the future. With this belief, we carried out the polyester recycling facility project with an investment of 10 million dollars. Thanks to this project, we broke new ground in Turkey and can produce polyester filament yarn from 100 % PET bottles. Having Starlinger at our side as a business partner gives us strength in our long-term journey towards sustainability.”
Breaking new ground in Turkey’s textile industry
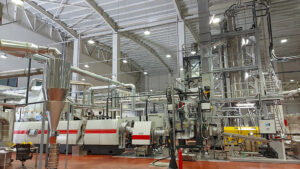
The Starlinger recoSTAR universal 165 H-VAC iV+, which is part of Korteks’ 10 million dollars investment in a new polymer recycling facility, took up operation in May 2021. It has a production capacity of 7,200 tons per year and currently processes clean in-house polyester fibers from production scrap together with washed post-consumer PET flakes at a ratio of 50/50. Korteks uses the polyester regranulate at a share of 100 % for its new polyester filament yarn line it is going to market under the name “TAÇ Reborn”. With this investment, the company has made an important step towards establishing a circular economy in the Turkish textile industry.
“We have been in extensive cooperation with Starlinger for a long time” said Barış Mert, General Manager of Korteks. “Thanks to their unique and innovative recycling technology we can offer new products in line with the circular economy model. That’s why, as Europe’s largest integrated and innovative polyester yarn producer, we are very pleased to work with Starlinger, the market leader in PET and polyester recycling and refining.”
Rapid Sleeve Changer: Finest melt filtration for perfect yarn
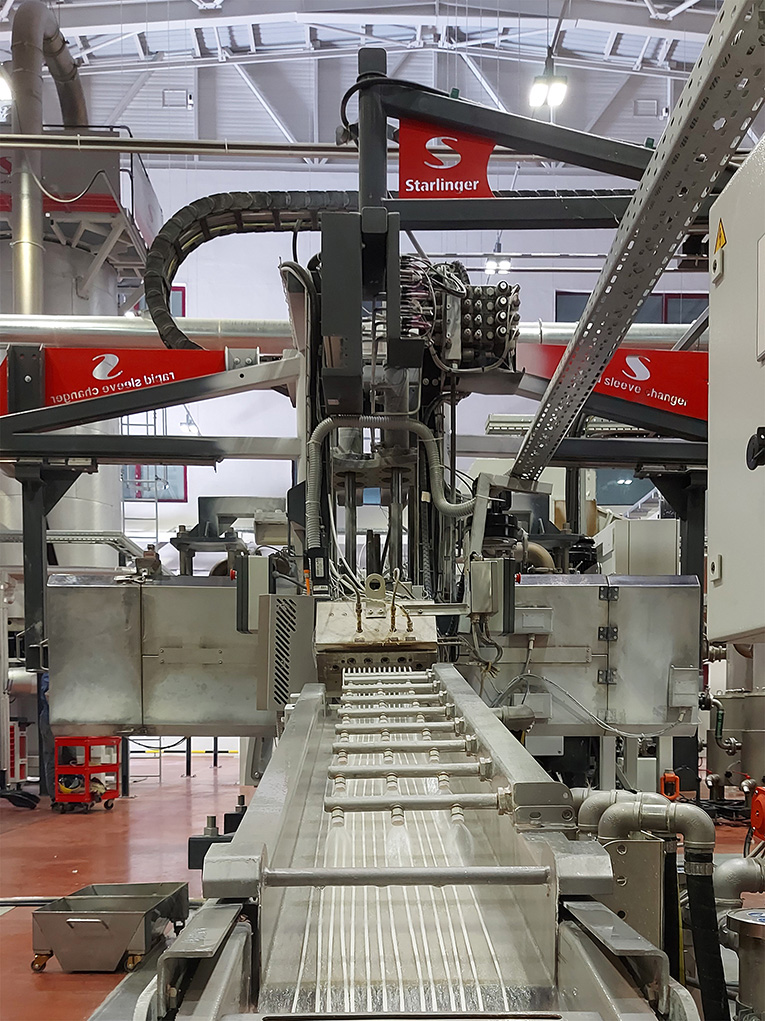
The Starlinger recycling line is the first of its kind in Turkey and is equipped with special components for filament yarn recycling. A RSC (Rapid Sleeve Changer) candle filter developed by Starlinger ensures finest melt filtration down to 15 μm. It has been specially designed for polyester recycling and reaches an output of 1000 kg/h. For continuous operation the filter elements are changed “on the fly” without interrupting production, which significantly limits melt loss.
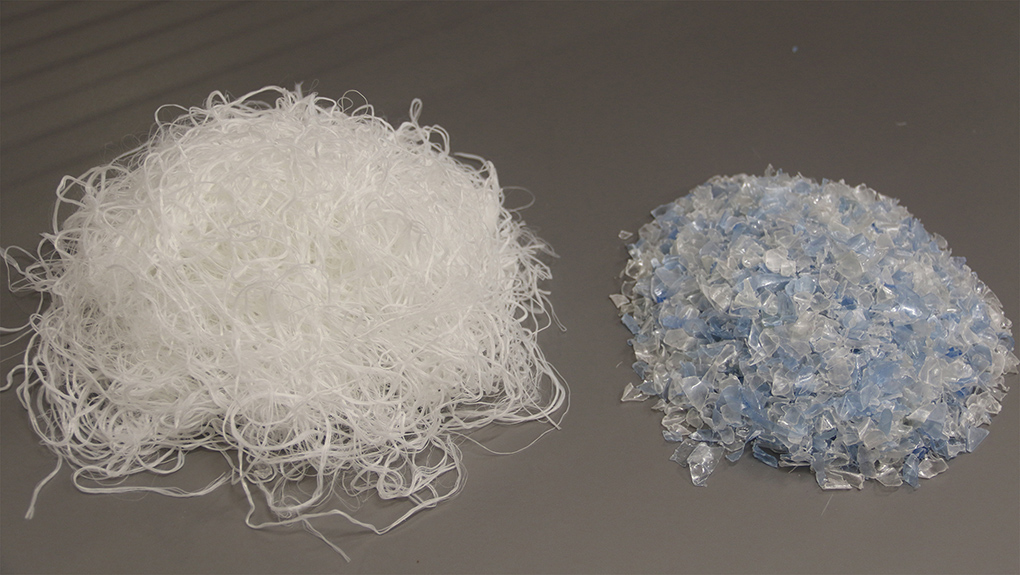
The viscoSTAR SSP unit at the end of the recycling process guarantees consistent IV increase according to the first-in-first-out principle. This makes sure that the produced regranulate has the ideal properties required for filament yarn production. The technical configuration of the line does not only allow the processing of a polyester fiber/PET flake mix as input materials, but also 100 % polyester filament scrap or 100 % PET bottle flakes.
With the new recycling facility, which comprises a total closed area of 17,000 m² and has a monthly production capacity of 600 tons, Korteks was able to reduce the production waste at its virgin PES yarn site to zero.
A paradigm shift in synthetic fiber production
“We are proud to be a partner in Korteks’ quest for more sustainability in the textile business”, said Paul Niedl, Commercial Head of Starlinger recycling technology. “Turkey is a significant global player in this industry. If more and more Turkish textile manufacturers start using recycled materials, this will be an important signal for the sector and a big step towards a circular economy. We support this development with our extensive know-how in synthetic fiber recycling and supply the fine-tuned and reliable recycling technology required in this field.”
Korteks expects the recycling market in general to grow as there is increased acceptance for recycled products in the society, and predicts the need for recycling solutions also for other synthetic and natural fibers.
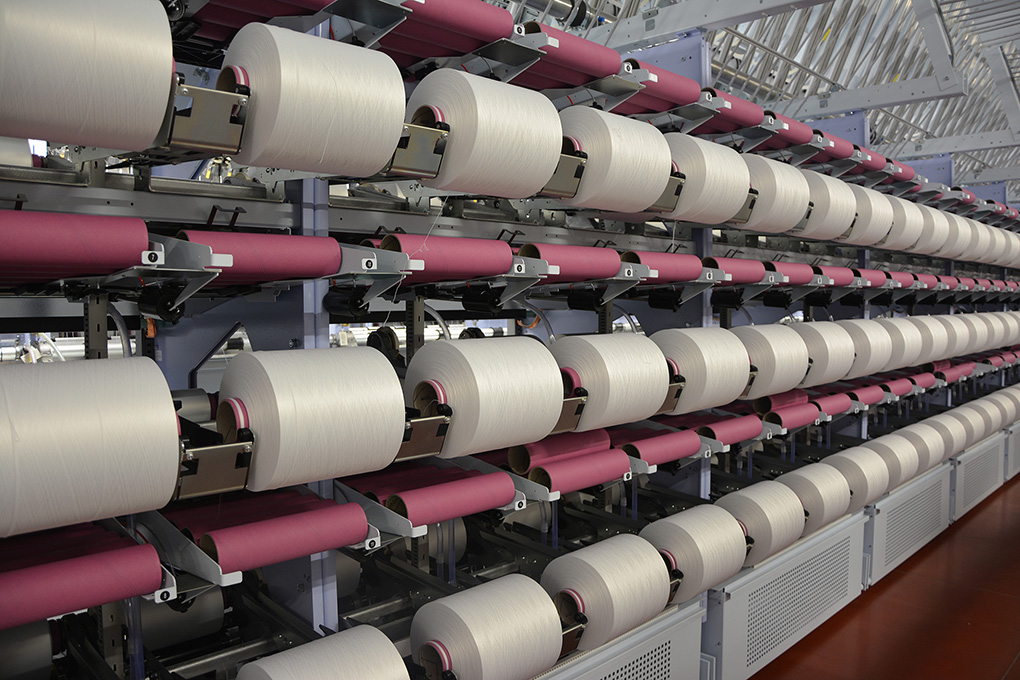
“At Korteks, we always aim at sustainable growth that reduces environmental impact and creates value. For this reason, we are gradually expanding our product range in sustainable and smart textiles every day”, said Barış Mert. “The period of the pandemic that the world has been going through has once again strikingly revealed the necessity of building a sustainable living together. The textile industry is also deeply affected by this big transformation on the globe. We believe that those who can manage this change well will also set the global textile agenda in the future. With this belief, we carried out the polyester recycling facility project with an investment of 10 million dollars. Thanks to this project, we broke new ground in Turkey and can produce polyester filament yarn from 100 % PET bottles. Having Starlinger at our side as a business partner gives us strength in our long-term journey towards sustainability.”
HolyGrail 2.0 reaches milestone with first prototype detection sorting unit
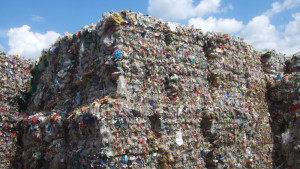
Developed by the machine vendor Pellenc ST and the digital watermarks technology provider Digimarc, the prototype, which combines the digital watermarks technology and NIR/VIS infrared for sorting of packaging waste, achieved a >95% ejection rate. This sorter is now ready to be installed in the Amager Resource Centre (ARC) in Copenhagen to start the semi-industrial test phase. Over the next four months, trials and demonstrations with around 125.000 pieces of packaging representing up to 260 different stock-keeping units (SKUs), all prepared by HolyGrail 2.0 members, will be held in Copenhagen. Engineers will test for several parameters including the speed and accuracy of the system, to ensure its ability to withstand the pressures of full-scale industrial operations.
If successful, digitally watermarked products could be introduced to store shelves in Denmark, France and Germany by the first half of 2022 for in-market demonstrations and industrial-scale trials.
HolyGrail 2.0 reaches milestone with first prototype detection sorting unit
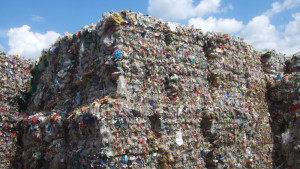
Developed by the machine vendor Pellenc ST and the digital watermarks technology provider Digimarc, the prototype, which combines the digital watermarks technology and NIR/VIS infrared for sorting of packaging waste, achieved a >95% ejection rate. This sorter is now ready to be installed in the Amager Resource Centre (ARC) in Copenhagen to start the semi-industrial test phase. Over the next four months, trials and demonstrations with around 125.000 pieces of packaging representing up to 260 different stock-keeping units (SKUs), all prepared by HolyGrail 2.0 members, will be held in Copenhagen. Engineers will test for several parameters including the speed and accuracy of the system, to ensure its ability to withstand the pressures of full-scale industrial operations.
If successful, digitally watermarked products could be introduced to store shelves in Denmark, France and Germany by the first half of 2022 for in-market demonstrations and industrial-scale trials.
Agilyx Corporation has been granted a patent continuation for its process of breaking down waste polystyrene into its chemical building block, styrene monomer.
Black Mass one of the hottest issues in battery recycling
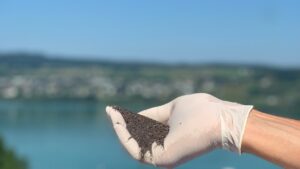
What is Black Mass actually?
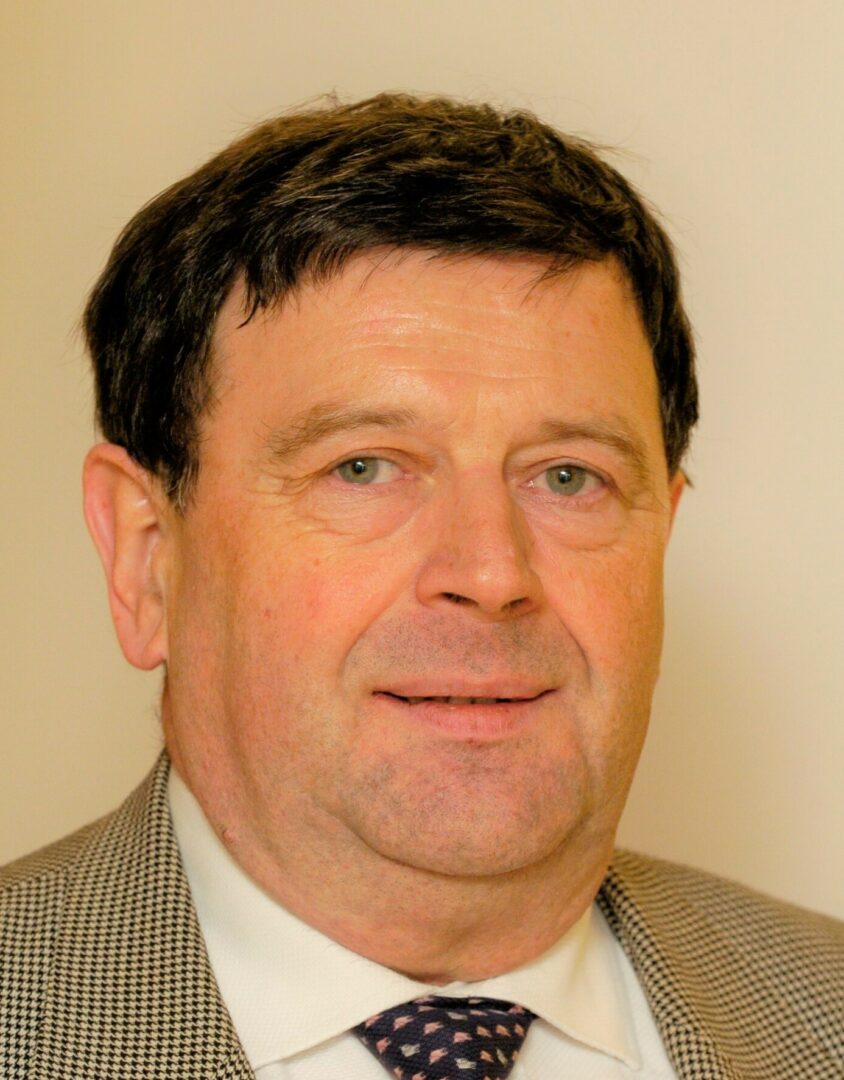
Jacques David: Black Mass is what you obtain once a battery has been processed for recycling. Batteries are composed of metals including lithium, manganese, cobalt, and nickel. Once a battery reaches the end of its service life, it is collected, dismantled, and shredded. The shredded material is then processed to produce “black mass”, which contains high amounts of these metals. These critical materials can then be extracted from the black mass and re-used in new battery production or in new products and/or applications.
Is there only one kind of Black Mass produced from one battery chemistry?
The composition of Black Mass is very diversified as the composition of Li-Ion batteries varies significantly from one producer to another and from one application to another. Different battery chemistries such as primary batteries and Ni-MH batteries also produce Black Mass. The composition of the Black Mass may vary significantly from OEM to OEM.
Can Black Mass processing be a profitable operation?
Depending on the content, yes it can. If a battery contains cobalt and nickel in certain quantities, then there will be no need to financially support the recycling operation.
Where are the major recycling facilities located today?
In China, Japan and South Korea there are large treatment facilities for batteries and battery waste, sometimes dealing with more than 50 000 tons per year. Many of these facilities have integrated the treatment of Black Mass mainly using a hydro-metallurgical process, which enables them to produce salts or metallic hydroxides which can be used as precursors.
What about European recyclers?
In Europe the recyclers have traditionally concentrated on battery recycling and have been waiting for bigger volumes of spent Li-ion batteries to become available before increasing capacity. Despite increasing volumes of Li-ion batteries needing recycling, the majority of the available tonnage comes from production waste from EV battery manufacturing or assembly facilities today. Challenges remain in order to reach the scale of Chinese capacity for Black Mass treatment.
What are the main challenges for EU operators?
European collectors and recyclers have always faced a lack of harmonization between different member States of the classification of spent Li-ion batteries. This creates a barrier to the development of the recycling market.
The expansion of Chinese battery and electric vehicle manufacturers operating in Europe will continue to give these companies a head start in the Black Mass recycling market here, and the developing practice of exporting Black Mass to Asia and the USA is certainly set to continue.
Is Black Mass waste?
Today, there is a lack of coherence between the various approaches to the definition of products coming from the treatment of waste batteries (Waste Directive Classification – Waste Batteries Directive – Chemicals Policy (EchA)). There is definitively a need for harmonization of the classification of spent batteries as a source of active materials to be used in new batteries or new applications. In the context of the EU Circular Economy Policy, the various precursors need to receive the same classification among EU Member States and among the international community.
Is there a Transport Regulation governing the transport and the export of spent batteries?
A harmonized International Transport Regulation (UN Model Regulation) regulates the transport of Dangerous Goods and another (Basel Convention) governs the transboundary movements of Hazardous Waste, such as the transport of certain spent batteries. Again, at international level there is a need to harmonize the conditions to transport the various types of “Black Mass”.