Used Textiles
Andritz to supply textile recycling Sweden
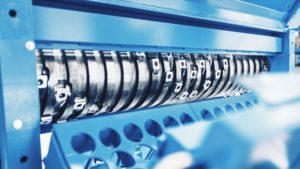
Core elements of the new recycling system will be Andritz ADuro shredders, which will shred used textiles in only one shredding step. With unique capabilities, the ADuro shredders cut the incoming material uniformly and cleanly while enabling a very high throughput. In the subsequent separation stages, contaminants like buttons and zippers will be removed from the shredded textiles. Renewcell uses this pre-treated material to produce a pure, natural dissolving pulp made from 100% recycled textiles.
In addition, the scope of supply includes additional key pieces of equipment. With the state-of-the-art equipment from Andritz, up to 60,000 tons of used textiles per year can be handled in the new recycling plant.
Renewcell, headquartered in Stockholm, Sweden, was founded in 2012 and is specialized in the recycling of textiles. The recycling technology employed by Renewcell dissolves used cotton and other cellulose fibers and transforms them into a new raw material, the so called Circulose® pulp, which is further used to make biodegradable virgin quality viscose or lyocell textile fibers for the fashion industry.
Urgent break with fast fashion needed in upcoming EU textile laws
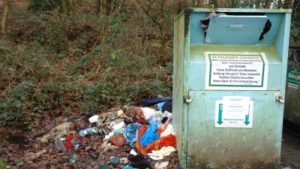
Some of Europe’s largest networks of green groups are joining forces to demand an end to fast fashion in the textile industry, one of the world’s largest industrial polluters.
As part of the Wardrobe Change campaign, NGOs are calling for new policies to stop runaway overproduction of textiles. Proposed measures include minimum standards for how long clothes should last, a ban on the destruction of unsold and returned goods, rules to verify and substantiate green claims, and ambitious targets for an absolute reduction in the amount of natural resources used across the supply chain.
The group is also calling for urgent rules on hazardous chemicals in fashion and for moves to combat environmental harm to include action to end labour rights’ violations in supply chains.
The call comes as clothing and textile production continues to soar despite an abundance of sustainability initiatives from major fashion brands and retailers.
The European Commission is currently gathering feedback from industry and civil society organisations, with the aim of putting forward new measures by the end of the year.
Emily Macintosh, Policy Officer for Textiles at the European Environmental Bureau (EEB), said: “We can’t ask people to do their part when it comes to sustainability if the multi-billion-dollar companies responsible for promoting such unsustainable consumption habits are not being held to account. EU laws should focus on reducing the amount of resources used across supply chains and on boosting the market for second-hand and repairable textiles. Fast fashion’s linear and exploitative business model must become a thing of the past.”
Valeria Botta, Programme Manager at ECOS – Environmental Coalition on Standards, added: “The EU can transform the way textile products are designed, making them sustainable by default. Our clothes need to last longer, be easier to mend and reuse, and be made without harmful materials and substances. To make sure textiles and their production are truly circular, we need ambitious EU laws that set minimum requirements, push the market towards the best option, and include ambitious binding targets for material and consumption footprints. The EU should grasp this opportunity to finally regulate this industry and inspire others.”
The NGOs’ position paper has four key demands:
- Make sustainable textile products the norm through high minimum design standards, better production processes, traceability, transparency and information disclosure, and banning the destruction of unsold and returned goods.
- Drive resource-sufficient textile consumption with rules on what reliable green claims can be made on products, harmonised labelling, and better information on the expected lifetime and repairability of a product.
- Leave the linear business model behind by taxing virgin resource use and making producers responsible for the products they put on the market from cradle to grave.
- Hold the EU textile industry accountable for its role in the world through a trade reset and strong human rights and environmental due diligence rules.
Fully circular clothing industry in the Netherlands is possible
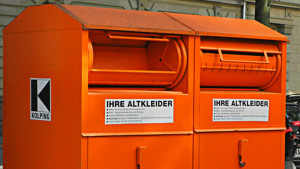
This is according to new research by Circle Economy’s Circular Jobs Initiative*, Putting circular textiles to work: The employment potential of circular clothing in the Netherlands. The report outlines three distinct circular scenarios—a shift in consumption patterns, prioritisation of reuse and repair, and upscaling of textile-to-textile recycling—through the lens of employment impacts, finding the second one to be most beneficial to the job market. But to realise such a scenario would require bridging current skills gaps, and re- and upskilling workers—bringing new careers, from (re)manufacturing designers to quality assessors to resale collection managers, to the fore.
The impact of the fashion industry on people and planet is well-known: the clothing industry accounts for around 5% of emissions worldwide, and workers around the globe are subject to unethical working conditions pervasive in the sector. And yet, the hunger for fast fashion is growing: in the Netherlands alone, residents purchase an average of one new garment per week, and around the world the equivalent of one truck load of clothing is burnt or incinerated every second. The need for a circular clothing industry—and especially one that benefits workers—is clear; but what skills do we need to get there?
Working in collaboration with the Goldschmeding Foundation, Circle Economy and HIVA dove into the intricacies of this question, with the aim of supporting national actors in the Dutch clothing value chain from linear to circular and supporting employment opportunities in the process.
Boosting clothing reuse and repair would see the greatest benefits, the report finds: a growing second-hand market and increased demand for repair and maintenance services could increase job creation in the industry by 25%—equal to 24,286 new full-time equivalents (FTEs) in repair and maintenance, 17,319 FTEs shifted from first- to second-hand sales and an additional 4,611 FTEs in second-hand sales. Some of the skills required for this scenario are already present in the Dutch labour market: repair and maintenance, logistics and procurement, manufacturing, management, sales and retail, waste management and industrial cleaning skills already crop up across the clothing value chain. As we progress towards a more circular system, the need for these skills will only become more prevalent—as will new jobs in technology, e-commerce and textile sorting, to better support repair and cycling. And what’s more, progressing to a fully circular sector that fulfills both environmental and social standards will need aspects of all three scenarios to be developed in combination, bringing additional skills to the fore.
The research leads collaborated with Amsterdam-based social enterprise Makers Unite to further explore skills gaps for their current and future business models. The organisation, which works with skilled newcomers to the Netherlands with a refugee background to create sustainable, upcycled products, hopes to convert to a fully circular business model. It notes the growing relevance of data scientists and analysts, sustainability and innovation managers, logistics and customer communications workers and the redevelopment of design, product development and tailoring roles.
‘I believe a transition towards a circular economy model starts by understanding how to make the best use of our existing resources: material and human. The innovation needed for the skillforce will create new opportunities for social inclusion to be fostered—and this is why we have focused our efforts on new business models.’ – Thami Schweichler, Managing Director at Makers Unite
The benefits of realising such a scenario are plentiful—but how can we get there? This will require committed coordination between relevant actors, from the Dutch government and private sector stakeholders to academia and education institutions—as well as action that ensures no worker is left behind or subject to unethical working conditions. Training and retraining must take a holistic approach and be directed at unemployed workers and those at risk of being phased out in addition to the employed workforce—and the role of vocational education and training must be recognised as essential to advancing the circular economy and building back better from the covid-19 pandemic.
Fully circular clothing industry in the Netherlands is possible
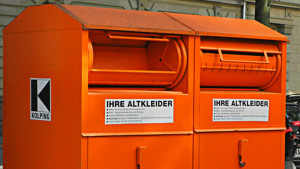
This is according to new research by Circle Economy’s Circular Jobs Initiative*, Putting circular textiles to work: The employment potential of circular clothing in the Netherlands. The report outlines three distinct circular scenarios—a shift in consumption patterns, prioritisation of reuse and repair, and upscaling of textile-to-textile recycling—through the lens of employment impacts, finding the second one to be most beneficial to the job market. But to realise such a scenario would require bridging current skills gaps, and re- and upskilling workers—bringing new careers, from (re)manufacturing designers to quality assessors to resale collection managers, to the fore.
The impact of the fashion industry on people and planet is well-known: the clothing industry accounts for around 5% of emissions worldwide, and workers around the globe are subject to unethical working conditions pervasive in the sector. And yet, the hunger for fast fashion is growing: in the Netherlands alone, residents purchase an average of one new garment per week, and around the world the equivalent of one truck load of clothing is burnt or incinerated every second. The need for a circular clothing industry—and especially one that benefits workers—is clear; but what skills do we need to get there?
Working in collaboration with the Goldschmeding Foundation, Circle Economy and HIVA dove into the intricacies of this question, with the aim of supporting national actors in the Dutch clothing value chain from linear to circular and supporting employment opportunities in the process.
Boosting clothing reuse and repair would see the greatest benefits, the report finds: a growing second-hand market and increased demand for repair and maintenance services could increase job creation in the industry by 25%—equal to 24,286 new full-time equivalents (FTEs) in repair and maintenance, 17,319 FTEs shifted from first- to second-hand sales and an additional 4,611 FTEs in second-hand sales. Some of the skills required for this scenario are already present in the Dutch labour market: repair and maintenance, logistics and procurement, manufacturing, management, sales and retail, waste management and industrial cleaning skills already crop up across the clothing value chain. As we progress towards a more circular system, the need for these skills will only become more prevalent—as will new jobs in technology, e-commerce and textile sorting, to better support repair and cycling. And what’s more, progressing to a fully circular sector that fulfills both environmental and social standards will need aspects of all three scenarios to be developed in combination, bringing additional skills to the fore.
The research leads collaborated with Amsterdam-based social enterprise Makers Unite to further explore skills gaps for their current and future business models. The organisation, which works with skilled newcomers to the Netherlands with a refugee background to create sustainable, upcycled products, hopes to convert to a fully circular business model. It notes the growing relevance of data scientists and analysts, sustainability and innovation managers, logistics and customer communications workers and the redevelopment of design, product development and tailoring roles.
‘I believe a transition towards a circular economy model starts by understanding how to make the best use of our existing resources: material and human. The innovation needed for the skillforce will create new opportunities for social inclusion to be fostered—and this is why we have focused our efforts on new business models.’ – Thami Schweichler, Managing Director at Makers Unite
The benefits of realising such a scenario are plentiful—but how can we get there? This will require committed coordination between relevant actors, from the Dutch government and private sector stakeholders to academia and education institutions—as well as action that ensures no worker is left behind or subject to unethical working conditions. Training and retraining must take a holistic approach and be directed at unemployed workers and those at risk of being phased out in addition to the employed workforce—and the role of vocational education and training must be recognised as essential to advancing the circular economy and building back better from the covid-19 pandemic.
Fully circular clothing industry in the Netherlands is possible
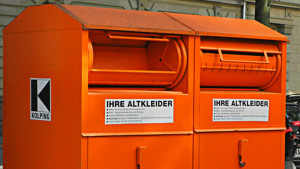
This is according to new research by Circle Economy’s Circular Jobs Initiative*, Putting circular textiles to work: The employment potential of circular clothing in the Netherlands. The report outlines three distinct circular scenarios—a shift in consumption patterns, prioritisation of reuse and repair, and upscaling of textile-to-textile recycling—through the lens of employment impacts, finding the second one to be most beneficial to the job market. But to realise such a scenario would require bridging current skills gaps, and re- and upskilling workers—bringing new careers, from (re)manufacturing designers to quality assessors to resale collection managers, to the fore.
The impact of the fashion industry on people and planet is well-known: the clothing industry accounts for around 5% of emissions worldwide, and workers around the globe are subject to unethical working conditions pervasive in the sector. And yet, the hunger for fast fashion is growing: in the Netherlands alone, residents purchase an average of one new garment per week, and around the world the equivalent of one truck load of clothing is burnt or incinerated every second. The need for a circular clothing industry—and especially one that benefits workers—is clear; but what skills do we need to get there?
Working in collaboration with the Goldschmeding Foundation, Circle Economy and HIVA dove into the intricacies of this question, with the aim of supporting national actors in the Dutch clothing value chain from linear to circular and supporting employment opportunities in the process.
Boosting clothing reuse and repair would see the greatest benefits, the report finds: a growing second-hand market and increased demand for repair and maintenance services could increase job creation in the industry by 25%—equal to 24,286 new full-time equivalents (FTEs) in repair and maintenance, 17,319 FTEs shifted from first- to second-hand sales and an additional 4,611 FTEs in second-hand sales. Some of the skills required for this scenario are already present in the Dutch labour market: repair and maintenance, logistics and procurement, manufacturing, management, sales and retail, waste management and industrial cleaning skills already crop up across the clothing value chain. As we progress towards a more circular system, the need for these skills will only become more prevalent—as will new jobs in technology, e-commerce and textile sorting, to better support repair and cycling. And what’s more, progressing to a fully circular sector that fulfills both environmental and social standards will need aspects of all three scenarios to be developed in combination, bringing additional skills to the fore.
The research leads collaborated with Amsterdam-based social enterprise Makers Unite to further explore skills gaps for their current and future business models. The organisation, which works with skilled newcomers to the Netherlands with a refugee background to create sustainable, upcycled products, hopes to convert to a fully circular business model. It notes the growing relevance of data scientists and analysts, sustainability and innovation managers, logistics and customer communications workers and the redevelopment of design, product development and tailoring roles.
‘I believe a transition towards a circular economy model starts by understanding how to make the best use of our existing resources: material and human. The innovation needed for the skillforce will create new opportunities for social inclusion to be fostered—and this is why we have focused our efforts on new business models.’ – Thami Schweichler, Managing Director at Makers Unite
The benefits of realising such a scenario are plentiful—but how can we get there? This will require committed coordination between relevant actors, from the Dutch government and private sector stakeholders to academia and education institutions—as well as action that ensures no worker is left behind or subject to unethical working conditions. Training and retraining must take a holistic approach and be directed at unemployed workers and those at risk of being phased out in addition to the employed workforce—and the role of vocational education and training must be recognised as essential to advancing the circular economy and building back better from the covid-19 pandemic.
New Project to drive Textile Recycling
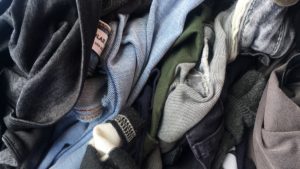
The Sorting for Circularity Project is driven by Fashion for Good with catalytic funding provided by Laudes Foundation and facilitated by brand partners, adidas, Bestseller, and Zalando, as well as Inditex as an external partner. Fashion for Good partners Arvind Limited, Birla Cellulose, Levi Strauss & Co., Otto and PVH Corp. are participating as part of the wider working group. Circle Economy leads the creation and implementation of the methodology, with support from Refashion, to assess textile waste composition. Both organisations build on their extensive experience from similar projects, such as the Interreg Fibersort Project and previous textile composition analyses.
The analysis will provide the most representative snapshot of textile waste composition generated in Europe. What is more, Fashion for Good and Circle Economy will map the current and future capabilities of textile recyclers in the region – illuminating crucial gaps between the sorting and recycling industry, and the innovation, investment and policy changes required to accelerate circularity.
Findings from this research will ultimately enable sorters to take action through the support of a digital platform that matches their textile waste with recyclers. This open-source platform will bring greater transparency, spark greater harmonisation between the industries, and ensure the learnings contribute to foundational change for the industry at large.
The project brings together the largest industrial textile sorters in the North-West European region; including the Boer Group, I:CO (a part of SOEX Group), JMP Wilcox (a part of Textile Recycling International) and Texaid, placing key industry players firmly at the heart of the project and driving the industry towards greater circularity.
The French accredited Extended Producer Responsibility (EPR) eco-organisation Refashion, a key project partner, provides input into the methodology and leads the NIR scanner calibration. Aligning the Sorting for Circularity Project with their own study in France ensures methodologies and findings can be standardised, compared and implemented on a larger scale.
New Project to drive Textile Recycling
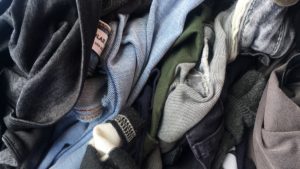
The Sorting for Circularity Project is driven by Fashion for Good with catalytic funding provided by Laudes Foundation and facilitated by brand partners, adidas, Bestseller, and Zalando, as well as Inditex as an external partner. Fashion for Good partners Arvind Limited, Birla Cellulose, Levi Strauss & Co., Otto and PVH Corp. are participating as part of the wider working group. Circle Economy leads the creation and implementation of the methodology, with support from Refashion, to assess textile waste composition. Both organisations build on their extensive experience from similar projects, such as the Interreg Fibersort Project and previous textile composition analyses.
The analysis will provide the most representative snapshot of textile waste composition generated in Europe. What is more, Fashion for Good and Circle Economy will map the current and future capabilities of textile recyclers in the region – illuminating crucial gaps between the sorting and recycling industry, and the innovation, investment and policy changes required to accelerate circularity.
Findings from this research will ultimately enable sorters to take action through the support of a digital platform that matches their textile waste with recyclers. This open-source platform will bring greater transparency, spark greater harmonisation between the industries, and ensure the learnings contribute to foundational change for the industry at large.
The project brings together the largest industrial textile sorters in the North-West European region; including the Boer Group, I:CO (a part of SOEX Group), JMP Wilcox (a part of Textile Recycling International) and Texaid, placing key industry players firmly at the heart of the project and driving the industry towards greater circularity.
The French accredited Extended Producer Responsibility (EPR) eco-organisation Refashion, a key project partner, provides input into the methodology and leads the NIR scanner calibration. Aligning the Sorting for Circularity Project with their own study in France ensures methodologies and findings can be standardised, compared and implemented on a larger scale.
Circular economy for the carpet industry
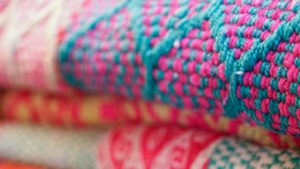
B.I.G. Yarns, a division of Beaulieu International Group, announces its latest development, Eqocycle, a fully recyclable PA6 yarn with 75% recycled content, offering the same high-quality performance of virgin PA6 yarn. The new recycled yarn mainly based on post-industrial waste supports contract, automotive and residential carpet manufacturers with a drop-in circular solution to reduce the ecological footprint of their end products.
Eqocycle is made with recycled granulates derived from pre-consumer recycled and regenerated PA6, certified by Control Union for Global Recycled Standard (GRS) Certification. The use of less virgin materials implicates a decrease of fossil fuels by 58% and a 27% decrease in energy consumption. On top, EqoCycle yarns allow a reduction of 37% of CO₂ eq./kg compared to the fossil based yarns. The environmental impacts of Eqocycle with 75% recycled content were calculated through an LCA analysis, verified according to ISO 14025 and EN 15804+A1 and published in an Environmental Product Declaration (EPD registration number S-P-02415).
Customers have the assurance that for every 1.000 tons of Eqocycle yarn, 13,562 barrels of oil are saved and 2.700 tons of CO2 emission are reduced, compared to PA6 traditionally made from virgin materials.
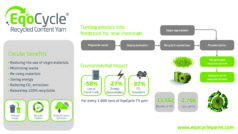
Emmanuel Colchen, General Manager Yarns Division, comments: “Eqocycle is a perfect example of how higher resource efficiency in our industry can promote greater circularity in our customers’ industries. Minimizing waste, re-using materials, and saving energy and carbon emissions in production, it provides our customers and carpet brands with a new sustainable alternative that won’t compromise their end-product performance but will support their increasing focus on CO2 reduction and global warming potential. All part of our wider commitment to encourage decoupling from the need for only virgin feedstocks and moving towards a circular economy for yarns and soft flooring industries.”
Eqocycle is the latest circular solution in B.I.G. Yarns’ PA6 portfolio, joining Eqobalance PA6, based on biomass balance renewable resources, which offers up to 75% CO2 reduction. Both exemplify the company’s on-going investment in developing new products that better serve customers’ needs in a sustainable way. B.I.G. Yarns fully pursues opportunities to support and solve the global environmental challenges through innovation, investment and collaboration, as part of its sincere belief in, and broader commitment to, Social Responsibility.
The innovation of Eqocycle and EqoBalance PA6 aligns with the company’s active integration of the UN Sustainable Development Goals (SDGs) into its business activities, creating value for customers and engaging employees and value chain partners.
Circular economy for the carpet industry
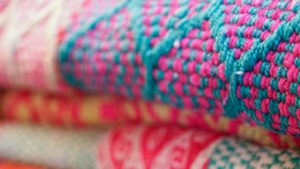
B.I.G. Yarns, a division of Beaulieu International Group, announces its latest development, Eqocycle, a fully recyclable PA6 yarn with 75% recycled content, offering the same high-quality performance of virgin PA6 yarn. The new recycled yarn mainly based on post-industrial waste supports contract, automotive and residential carpet manufacturers with a drop-in circular solution to reduce the ecological footprint of their end products.
Eqocycle is made with recycled granulates derived from pre-consumer recycled and regenerated PA6, certified by Control Union for Global Recycled Standard (GRS) Certification. The use of less virgin materials implicates a decrease of fossil fuels by 58% and a 27% decrease in energy consumption. On top, EqoCycle yarns allow a reduction of 37% of CO₂ eq./kg compared to the fossil based yarns. The environmental impacts of Eqocycle with 75% recycled content were calculated through an LCA analysis, verified according to ISO 14025 and EN 15804+A1 and published in an Environmental Product Declaration (EPD registration number S-P-02415).
Customers have the assurance that for every 1.000 tons of Eqocycle yarn, 13,562 barrels of oil are saved and 2.700 tons of CO2 emission are reduced, compared to PA6 traditionally made from virgin materials.
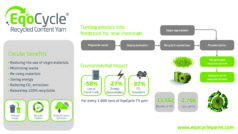
Emmanuel Colchen, General Manager Yarns Division, comments: “Eqocycle is a perfect example of how higher resource efficiency in our industry can promote greater circularity in our customers’ industries. Minimizing waste, re-using materials, and saving energy and carbon emissions in production, it provides our customers and carpet brands with a new sustainable alternative that won’t compromise their end-product performance but will support their increasing focus on CO2 reduction and global warming potential. All part of our wider commitment to encourage decoupling from the need for only virgin feedstocks and moving towards a circular economy for yarns and soft flooring industries.”
Eqocycle is the latest circular solution in B.I.G. Yarns’ PA6 portfolio, joining Eqobalance PA6, based on biomass balance renewable resources, which offers up to 75% CO2 reduction. Both exemplify the company’s on-going investment in developing new products that better serve customers’ needs in a sustainable way. B.I.G. Yarns fully pursues opportunities to support and solve the global environmental challenges through innovation, investment and collaboration, as part of its sincere belief in, and broader commitment to, Social Responsibility.
The innovation of Eqocycle and EqoBalance PA6 aligns with the company’s active integration of the UN Sustainable Development Goals (SDGs) into its business activities, creating value for customers and engaging employees and value chain partners.
Circular economy for the carpet industry
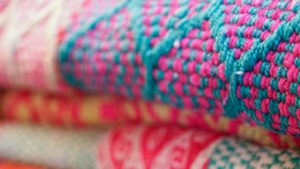
B.I.G. Yarns, a division of Beaulieu International Group, announces its latest development, Eqocycle, a fully recyclable PA6 yarn with 75% recycled content, offering the same high-quality performance of virgin PA6 yarn. The new recycled yarn mainly based on post-industrial waste supports contract, automotive and residential carpet manufacturers with a drop-in circular solution to reduce the ecological footprint of their end products.
Eqocycle is made with recycled granulates derived from pre-consumer recycled and regenerated PA6, certified by Control Union for Global Recycled Standard (GRS) Certification. The use of less virgin materials implicates a decrease of fossil fuels by 58% and a 27% decrease in energy consumption. On top, EqoCycle yarns allow a reduction of 37% of CO₂ eq./kg compared to the fossil based yarns. The environmental impacts of Eqocycle with 75% recycled content were calculated through an LCA analysis, verified according to ISO 14025 and EN 15804+A1 and published in an Environmental Product Declaration (EPD registration number S-P-02415).
Customers have the assurance that for every 1.000 tons of Eqocycle yarn, 13,562 barrels of oil are saved and 2.700 tons of CO2 emission are reduced, compared to PA6 traditionally made from virgin materials.
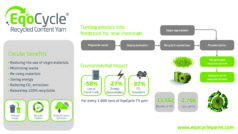
Emmanuel Colchen, General Manager Yarns Division, comments: “Eqocycle is a perfect example of how higher resource efficiency in our industry can promote greater circularity in our customers’ industries. Minimizing waste, re-using materials, and saving energy and carbon emissions in production, it provides our customers and carpet brands with a new sustainable alternative that won’t compromise their end-product performance but will support their increasing focus on CO2 reduction and global warming potential. All part of our wider commitment to encourage decoupling from the need for only virgin feedstocks and moving towards a circular economy for yarns and soft flooring industries.”
Eqocycle is the latest circular solution in B.I.G. Yarns’ PA6 portfolio, joining Eqobalance PA6, based on biomass balance renewable resources, which offers up to 75% CO2 reduction. Both exemplify the company’s on-going investment in developing new products that better serve customers’ needs in a sustainable way. B.I.G. Yarns fully pursues opportunities to support and solve the global environmental challenges through innovation, investment and collaboration, as part of its sincere belief in, and broader commitment to, Social Responsibility.
The innovation of Eqocycle and EqoBalance PA6 aligns with the company’s active integration of the UN Sustainable Development Goals (SDGs) into its business activities, creating value for customers and engaging employees and value chain partners.